Yes, it is possible to powder coat magnesium, making it an effective coating option for this material. Powder coating provides a durable and protective finish, improving the aesthetics and corrosion resistance of magnesium components.
It involves electrostatically applying a dry powder to the surface, followed by a curing process to create a hard, consistent coating. Powder coating offers several advantages, such as a wide range of color options, environmental sustainability, and cost-effectiveness. It is commonly used in industries like automotive, aerospace, and electronics for various magnesium applications.
However, it is important to adhere to specific guidelines and pretreatment processes to ensure successful powder coating on magnesium.

Understanding The Basics Of Magnesium Powder Coating
Magnesium is a versatile material that has gained much attention in various industries for its lightweight and durable properties. But can you powder coat magnesium? In this article, we will delve into the world of magnesium powder coating, exploring what it is, why it is popular, and the advantages and challenges associated with it.
What Is Powder Coating And How Does It Work?
Powder coating is a process widely used to apply a protective and decorative finish to various materials, including metals, plastics, and ceramics. Unlike traditional liquid paint, the coating is applied as a dry powder and is cured through heating. This method offers several advantages, such as improved durability, resistance to corrosion and wear, and a wide range of color options.
Read More Details About What Powder Coating Is and How It Works.
Why Is Powder Coating A Popular Choice For Various Materials?
Powder coating has gained immense popularity as a preferred finishing method for a wide range of materials due to its numerous benefits. First and foremost, it provides enhanced protection against corrosion, UV rays, and impacts, making it suitable for both indoor and outdoor applications.
Moreover, the dry powder application offers superior coverage and consistency, resulting in a smooth and flawless finish. Powder coating is also an environmentally friendly option as it does not contain any volatile organic compounds (VOCs), making it safer for both the applicator and the environment.
Introducing Magnesium As A Potential Material For Powder Coating
Magnesium has recently emerged as an intriguing material for powder coating applications. With its impressive strength-to-weight ratio, this lightweight metal has become increasingly popular in industries such as automotive, aerospace, and electronics. Powder coating magnesium presents an opportunity to further enhance its durability and resistance to external factors. Whether it’s protecting automobile components from corrosion or providing a sleek, decorative finish for consumer electronics, powder coating offers magnesium a new dimension of versatility.

Exploring The Advantages And Challenges Of Powder Coating Magnesium
While powder coating can certainly enhance the properties of magnesium, it is important to recognize the unique advantages and challenges associated with this process. Some potential advantages include improved resistance to corrosion, chemicals, and extreme temperatures. Additionally, powder coating allows for a wide selection of colors and finishes, enabling customization options for different applications.
It is essential to be aware of the challenges as well, such as the need for proper surface preparation to ensure adhesion, as well as the potential for hydrogen embrittlement during the powder coating process.
Powder coating offers exciting opportunities for the application of magnesium as a versatile and lightweight material. By understanding the basics of powder coating and exploring its advantages and challenges, we can unlock the full potential of magnesium and create durable, aesthetically pleasing products across various industries.
Factors To Consider Before Powder Coating Magnesium
When it comes to powder coating magnesium, there are several important factors that need to be considered. Assessing the chemical and physical properties of magnesium, understanding its unique characteristics, evaluating the surface preparation requirements, and identifying potential risks and safety considerations are all crucial steps to ensure a successful powder coating process. Let’s take a closer look at each of these factors in detail:
Assessing The Chemical And Physical Properties Of Magnesium
Before powder coating magnesium, it’s essential to assess its chemical and physical properties. Magnesium is a lightweight metal with a low density, making it highly desirable for various applications. However, its reactivity with air and moisture can pose challenges during the coating process. Understanding the chemical composition and reactivity of magnesium is key to selecting the appropriate powder coating material and process.

Understanding The Unique Characteristics Of Magnesium That Impact Powder Coating
Magnesium possesses unique characteristics that can significantly impact the powder coating process. For instance, magnesium has a high affinity for oxygen, making proper surface preparation crucial to achieve a strong bond between the powder coating and the magnesium substrate. It’s important to take into account factors such as the thermal conductivity and expansion coefficient of magnesium to prevent potential issues, such as blistering or cracking, during the curing process.
Evaluating The Surface Preparation Requirements For Magnesium
Surface preparation is paramount when it comes to powder coating magnesium. The surface must be thoroughly cleaned and free from any contaminants, such as dirt, oils, or oxides, which can hinder the adhesion of the powder coating. To ensure optimal surface preparation, methods like chemical cleaning, mechanical abrasion, or solvent degreasing may be employed. It’s crucial to follow the specific guidelines recommended by the powder coating manufacturer to achieve the desired result.

Identifying Potential Risks And Safety Considerations When Powder Coating Magnesium
Working with magnesium powder coating presents certain risks and safety considerations that need to be addressed. Magnesium is highly flammable and can ignite at relatively low temperatures. It’s essential to establish proper ventilation systems, use suitable fire suppression equipment, and ensure employees are trained in handling magnesium safely. Moreover, protective measures, such as wearing appropriate safety gear like gloves, goggles, and fire-resistant clothing, should be implemented to minimize any potential hazards.
Techniques For Powder Coating Magnesium
When it comes to powder coating, magnesium surfaces require special attention due to their unique chemical composition and reactive nature. Implementing the right techniques is crucial to ensure a perfect and durable powder coating finish on magnesium components. In this blog post, we will explore the key techniques for powder coating magnesium, including pre-treatment methods, selecting the right powder coating material, application methods, and curing and finishing techniques.
Pre-treatment Methods For Magnesium Surfaces Before Powder Coating
Proper pre-treatment of magnesium surfaces is essential to improve adhesion and corrosion resistance of the powder coating. Here are some recommended pre-treatment methods:
- De-greasing: Before powder coating, it is crucial to remove any oil, grease, or contaminants from the magnesium surface. This can be achieved through solvent cleaning or alkaline cleaning solutions.
- Etching: Magnesium surfaces should undergo an etching process to improve adhesion. Acid etching or chemical conversion coatings can be used to create a suitable surface for the powder coating to bond effectively.
- Conversion coating: Applying a conversion coating, such as chromate conversion coating or phosphating, can significantly enhance the corrosion resistance of the magnesium surface.
Selecting The Right Powder Coating Material For Magnesium

Choosing the appropriate powder coating material is crucial to ensure compatibility with magnesium and achieve the desired aesthetics and performance. Consider the following factors when selecting a powder coating material for magnesium:
- Chemical resistance: Magnesium can be sensitive to certain chemicals, so it is important to choose a powder coating material that offers good chemical resistance to protect the surface from deterioration.
- Flexibility: Magnesium components may experience bending or flexing during use. Opt for a powder coating material with high flexibility to prevent cracking or peeling.
- Temperature resistance: Some applications may subject the powder coated magnesium components to high temperatures. Select a powder coating material that can withstand the intended operating temperatures without degradation.
- Appearance: Consider the desired color, texture, and gloss level of the powder coated magnesium surface. Polyester powder coating offers various finishes, allowing for customization.
Application Methods For Powder Coating Magnesium
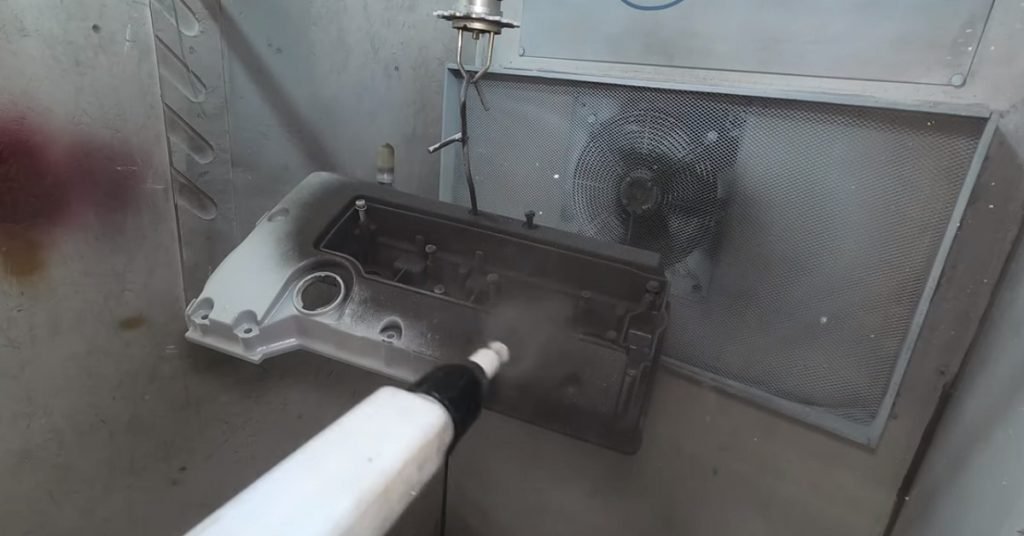
The application of powder coating onto magnesium surfaces plays a crucial role in achieving a uniform and durable finish. The following methods are commonly used for powder coating magnesium:
- Electrostatic spray: Electrostatic spray guns charge the powder particles, enabling them to adhere to the grounded magnesium surface. This method provides excellent coverage and transfer efficiency.
- Fluidized bed: The fluidized bed method involves immersing the preheated magnesium component into a container of fluidized powder particles. The powder particles adhere to the heated surface, creating a thick and even coating.
- Electrostatic fluidized bed: Similar to fluidized bed, this method involves using an electrostatic charge to enhance powder adhesion. It offers improved control over the powder thickness and is commonly used for intricate or complex-shaped magnesium parts.
Curing And Finishing Techniques For Powder Coated Magnesium Surfaces
Proper curing and finishing techniques are crucial to achieve the desired appearance and performance of the powder coated magnesium surface. Consider the following techniques:
- Curing: The powder-coated magnesium component should be cured at a temperature of generally 350-400°F for 10 to 15 minutes and must also follow the manufacturer’s instructions. This typically involves subjecting it to elevated temperatures to allow the powder to melt, flow, and create a durable coating.
- Finishing options: Depending on the desired appearance, additional finishing techniques can be employed. These may include clear coats, top coats, or additives to enhance specific characteristics like UV resistance or texture.
By following these techniques for powder coating magnesium, you can achieve a high-quality, long-lasting finish on magnesium components, enhancing their aesthetics and performance while protecting against corrosion and wear.
Overcoming Challenges In Powder Coating Magnesium
Powder coating is a popular method for adding a durable and attractive finish to various metals. However, when it comes to powder coating magnesium, a few challenges present themselves. Adhesion and coating thickness, corrosion risk, gas pore formation, and achieving a smooth finish are some of these challenges.
Addressing Issues Related To Adhesion And Coating Thickness
When powder coating magnesium, ensuring proper adhesion and achieving the desired coating thickness are vital for the durability and appearance of the finished product. Magnesium’s unique properties can make it challenging for the powder coating to adhere effectively. To address this issue, several steps can be taken:
- Preparing the surface: Thoroughly clean the magnesium surface using a degreaser or solvent to remove any oils, dirt, or contaminants that may hinder adhesion.
- Providing an ideal surface profile: Abrasive blasting or chemical etching can help create a roughened surface profile that provides better adhesion for the powder coating material.
- Using appropriate primers: Applying a primer specifically formulated for magnesium can improve adhesion and help achieve the desired coating thickness.
Mitigating The Risk Of Corrosion In Powder Coated Magnesium
Magnesium is susceptible to corrosion, and the powder coating serves as a protective barrier against this damaging effect. However, there are measures that can be taken to enhance the resistance of powder coated magnesium against corrosion:
- Selecting the right powder coating material: Choosing a powder coating material with excellent corrosion resistance properties specifically designed for use on magnesium can minimize the risk of corrosion.
- Proper pretreatment: Implementing a thorough cleaning and pretreatment process before powder coating, such as using conversion coatings, can improve the bond between the magnesium substrate and the powder coating, enhancing the corrosion resistance.
- Regular inspections and maintenance: Conduct periodic inspections to identify any signs of corrosion or damage to the powder coating. Promptly addressing any issues can help prevent the corrosion from spreading and compromising the protective coating.
Minimizing The Formation Of Gas Pores And Defects During The Coating Process
Gas pore formation and other defects can affect the appearance and integrity of the powder coated magnesium. While it is challenging to completely eliminate these issues, adopting the following strategies can minimize their occurrence:
- Baking and degassing: Preheating the magnesium substrate before the powder coating process and incorporating a proper degassing step can help release trapped gases and minimize pore formation.
- Optimizing powder coating application parameters: Adjusting the powder coating application parameters, such as air pressure, spray gun distance, and curing time, can help control the formation of gas pores and defects.
- Proper film thickness control: Ensuring proper film thickness through proper powder coating application techniques and using thickness measurement tools can contribute to reducing the likelihood of gas pore formation.
Strategies For Achieving A Smooth And Durable Powder Coated Finish On Magnesium
Obtaining a smooth and durable powder coated finish on magnesium requires attention to detail and the implementation of effective strategies. Here are some recommendations to achieve optimal results:
- Appropriate powder coating material selection: Selecting a powder coating material with good flow and leveling properties specifically designed for magnesium can help achieve a smoother finish.
- Optimal curing conditions: Following the manufacturer’s curing recommendations and ensuring accurate temperature and time control during the curing process can contribute to a more durable and aesthetically pleasing coating.
- Proper equipment maintenance: Regularly cleaning and maintaining spray guns, booths, and other powder coating equipment can prevent the accumulation of contaminants and ensure consistent coating application.
By addressing the challenges related to adhesion, coating thickness, corrosion, gas pore formation, and finish quality, you can achieve excellent results when powder coating magnesium. With careful preparation, proper material selection, and attention to detail, your powder coated magnesium projects can stand the test of time, showcasing both durability and visual appeal.
Best Practices For Powder Coating Magnesium
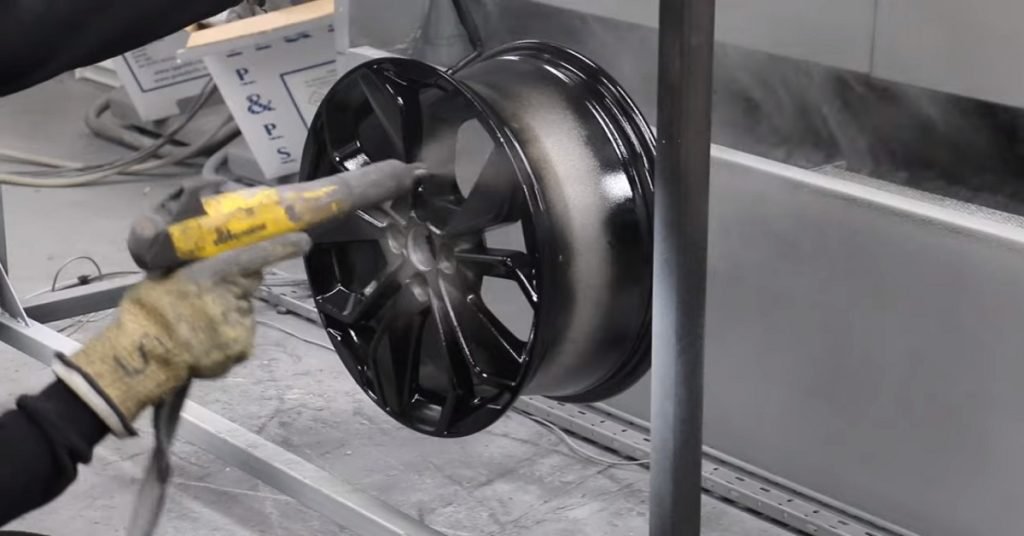
Powder coating has become a popular choice for protecting and enhancing the appearance of various metal components. However, when it comes to powder coating magnesium, there are specific considerations and best practices that must be followed to ensure successful and durable finishes.
Proper Handling And Storage Of Magnesium Components For Powder Coating
Magnesium, being a highly reactive metal, requires careful handling and storage to prevent oxidation and contamination. Here are some essential guidelines to follow:
- Store magnesium components in a dry and moisture-free environment to minimize the chances of oxidation.
- Handle magnesium with clean gloves to prevent contamination from oils, grease, or dirt.
- Avoid prolonged exposure to humidity or water, as it can corrode the magnesium surface.
- Ensure adequate ventilation in the powder coating area to remove any fumes that may be released during curing.
Quality Control Measures For Ensuring Consistent And Reliable Powder Coated Magnesium Finishes
Consistency and reliability are crucial aspects of powder coated magnesium finishes. Implementing quality control measures can help achieve the desired results consistently:
- Thoroughly clean the surface of the magnesium component before powder coating to remove any contaminants.
- Perform regular checks on the powder coating equipment, such as the spray gun and booth, to ensure proper functioning and consistent application of powder.
- Regularly monitor the curing process to ensure the correct temperature and duration, as improper curing can lead to defects and reduced adhesion.
- Implement routine checks and inspections of the coated magnesium surfaces to identify any imperfections or areas requiring touch-ups.
Maintenance And Care Tips For Extending The Lifespan Of Powder Coated Magnesium Surfaces

Proper maintenance and care can significantly extend the lifespan and appearance of powder coated magnesium surfaces. Consider the following tips:
- Regularly clean the powder coated magnesium parts using mild soap, water, and a soft cloth or sponge.
- Avoid abrasive cleaners or brushes that can scratch the surface and compromise the powder coating integrity.
- Inspect the coated surfaces for any signs of damage, such as chips or scratches, and promptly address them to prevent further deterioration.
- Whenever possible, protect the powder coated surfaces from prolonged exposure to direct sunlight or harsh environmental conditions, as these factors can degrade the coating over time.
Case Studies And Success Stories Of Powder Coating Magnesium In Different Industries
Multiple industries have successfully utilized powder coating on magnesium components. Here are a few case studies showcasing the benefits and applications:
Industry | Application | Results |
---|---|---|
Automotive | Powder coated magnesium alloy wheels | Enhanced durability, corrosion resistance, and aesthetic appeal. |
Aerospace | Powder coated magnesium aircraft components | Improved protection against high temperatures, chemicals, and wear. |
Sports and Recreation | Powder coated magnesium bicycle frames | Lightweight, durable finish with customizable colors and designs. |
These success stories demonstrate the versatility and advantages of powder coating magnesium in different sectors.
Frequently Asked Questions For Can You Powder Coat Magnesium?
How Do You Prepare Magnesium For Powder Coating?
Preparing magnesium for powder coating involves five key steps:
- Clean the magnesium surface to remove any dirt, grease, or contaminants.
- Etch the surface using a suitable chemical solution to promote adhesion.
- Rinse the magnesium thoroughly to remove any residual chemicals.
- Apply a conversion coating or primer to further enhance adhesion and corrosion resistance.
- Finally, cure the powder coating according to the manufacturer’s instructions for a durable finish.
Can You Sandblast Magnesium Wheels?
Yes, you can sandblast magnesium wheels. Sandblasting is a common method for removing dirt, paint, and rust from wheels. It is important to follow proper safety guidelines and use the correct equipment to prevent any damage to the wheels.
Can You Paint Magnesium Wheels?
Yes, you can paint magnesium wheels.
Final Thoughts
Powder coating magnesium presents both advantages and challenges. While the durable finish, corrosion resistance, and aesthetic appeal make powder coating an attractive option, the potential for flammability and porosity make it crucial to exercise caution. By understanding the unique characteristics of magnesium and working with experienced professionals, it is possible to achieve successful powder coating results.
Proper surface preparation, temperature control, and utilization of appropriate powder coatings are essential for a long-lasting, high-quality finish.