Powder coating defects can occur due to various reasons in the application process, such as insufficient cleaning, improper curing, or inadequate powder base. These issues can result in defects like orange peel, blistering, or color variation.
We will explore common powder coating defects, their causes, and potential solutions to achieve a high-quality finish for your coated products. Understanding these defects and their root causes will help you address them effectively and maintain a flawless powder coating surface that meets your desired standards of durability and aesthetics.
With this knowledge, you can address issues decisively and achieve flawless powder coated finishes. So let’s get started!

Introduction To Powder Coating Defects
Powder coating is a popular and effective method of adding durability and aesthetic appeal to various products. It involves applying a dry powder to a surface and then curing it under heat to create a hard and protective coating.
However, even with careful application, defects can occur during the powder coating process. These defects not only affect the visual appearance of the coated products but also have the potential to compromise their overall quality and performance.
Why Understanding Powder Coating Defects Is Important
Understanding powder coating defects is crucial for various reasons. By identifying and addressing these defects, manufacturers can ensure that their products meet the highest quality standards and deliver optimal performance. Here are a few key reasons why understanding powder coating defects is essential:
Quality assurance: Powder coating defects can lead to the production of subpar products. By identifying and rectifying these defects, manufacturers can maintain consistency and meet customer expectations.
Cost reduction: Identifying and addressing defects early in the production process can help save costs associated with rework or rejection of defective products.
Customer satisfaction: By delivering products with a flawless coating, manufacturers can enhance customer satisfaction and build a positive reputation for their brand.
Longevity and durability: Powder coating defects can compromise the protective properties of the coating, reducing the longevity and durability of the coated products. Understanding and addressing these defects ensures the longevity and durability of the finished items.
How Powder Coating Defects Can Affect The Overall Quality Of Products
The presence of powder coating defects can significantly impact the overall quality of products. These defects can manifest in various forms, including uneven coating thickness, adhesion issues, pinholes, orange peel effect, color inconsistencies, and more.
Here’s how the different types of defects can affect the overall quality of products:
Uneven coating thickness: Inconsistent coating thickness can result in an uneven appearance and compromised protection. It can also lead to reduced corrosion resistance, making the product susceptible to premature deterioration.
Adhesion issues: Poor adhesion between the coating and substrate can result in flaking, chipping, or peeling of the coating, leaving the product vulnerable to corrosion and aesthetic degradation.
Pinholes: Pinholes are small gaps or voids in the coating that can expose the substrate to moisture and corrosion. They can also cause aesthetic issues by creating an uneven texture or appearance.
Orange peel effect: The orange peel effect refers to a textured surface resembling the skin of an orange. This defect can occur due to improper curing or incorrect spraying techniques, resulting in an undesirable appearance.
Color inconsistencies: Inaccurate color matching or inconsistent application can lead to color deviations. This defect can affect the aesthetics and visual appeal of the finished product, especially when color uniformity is desired.
By understanding the different types of powder coating defects and their potential impact on product quality, manufacturers can take proactive measures to address and eliminate these issues, ensuring the production of high-quality and visually appealing products.
8 Common Types Of Powder Coating Defects
Before diving into details, here is a quick reference table summarizing the most common powder coating defects, their causes, and solutions:
Defect | Causes | Solutions |
---|---|---|
Overspraying | Excessive powder output, improper gun settings/distance | Adjust settings, optimal distance, multiple thin coats |
Pinholes And Pitting | Contaminants, poor adhesion, moisture | Thorough pretreatment, proper powder application |
Orange Peel | Improper cure, poor flow, too much powder | Optimize cure, adjust gun settings, proper thickness |
Fish Eye defect | Oil, silicone or other contaminants | Keep powder clean, test for contaminants |
Blistering | Moisture, contaminants, poor prep or curing | Clean/pretreat thoroughly, proper cure schedule |
Poor Adhesion | Contaminants, inadequate profile, incompatibility | Test compatibility, proper surface prep |
Color Variance | Poor mixing, contamination, application issues | Improve mixing, quality control, consistency |
Cracking/Chipping | Excess thickness, poor curing, inadequate flexibility | Control thickness, optimize curing, suitable powder choice |
Now let’s explore each of these prevalent powder coating defects in more detail.
Powder coating is a popular choice for achieving a durable and aesthetically pleasing finish on a wide range of surfaces. However, like any coating process, it is not immune to defects that can affect the quality and performance of the finished product.
Understanding the common types of powder coating defects and their causes is essential for ensuring a high-quality coating. Now, we will explore 8 common defects: Overspraying, pinholes and pitting, orange peel, fish eyes, blistering, poor adhesion, color variance, and cracking or chipping.
#1 Overspraying Defects
Overspraying occurs when an excessive amount of powder is applied, resulting in an uneven or overly thick coating. It leads to texture and appearance problems.
What Causes Overspraying?
Overspraying is generally caused by:
- Excessive powder output from the gun due to high kV settings or air pressure.
- Incorrect gun-to-part distance being too far away.
- Operator moving the gun too fast over the surface.
- Poor technique by the operator leading to inconsistent passes.
Preventing Overspraying
Overspraying can be prevented by:
- Adjusting gun settings to lower powder output – reduce kV level and air pressure.
- Maintaining proper gun distance from the part per specifications.
- Moving the gun at optimal traverse speed for even coverage.
- Applying multiple thinner coats rather than one heavy coat.
- Proper training for operators on spray techniques.
#2 Pinholes And Pitting
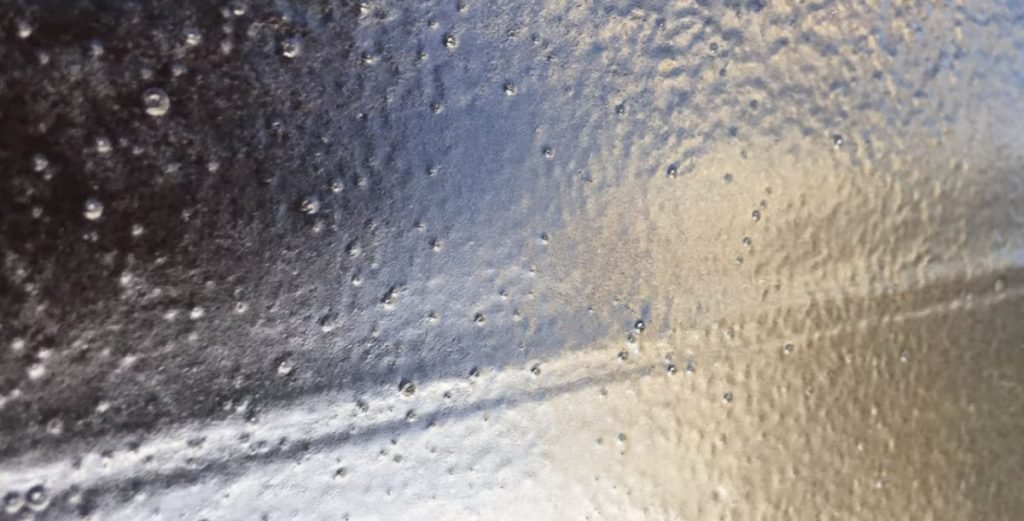
Tiny voids and craters called pinholes are another prevalent powder coating problem. These small holes penetrate through the coating, exposing the metal underneath. Even a few pinholes can lead to corrosion and performance issues..
What Causes Pinholes?
Pinholes often arise when the powder coating doesn’t fully wet and adhere to the substrate. Typical causes include:
- Oil, grease, rust, mill scale or other contaminants still present on the substrate.
- Inadequate surface profile unable to support mechanical bonding.
- Moisture on the metal reacting with curing temperatures to form gasses.
- Insufficient powder coating thickness in high-risk corner and edge areas.
Essentially any foreign matter or lack of adhesion can lead to voids forming as the coating cures.
Eliminating Pinhole Defects
Achieving excellent surface preparation and powder application is key to preventing pinholes:
- Thoroughly degrease and clean the substrate first to remove any possible contaminants like oil or dirt.
- Create proper surface profile through abrasive blasting, chemical etching, or sanding to enable adhesion.
- Preheat the substrate to drive off any residual moisture before powder coating.
- Apply sufficiently thick and uniform powder layers, especially on edges and openings prone to pinholes.
- Use gel coating products designed to help bridge high-risk gaps and resist pinholing.
By following best practices for pretreatment and powder application, you can virtually eliminate pinhole defects and get optimal coating coverage.
#3 Orange Peel Effect
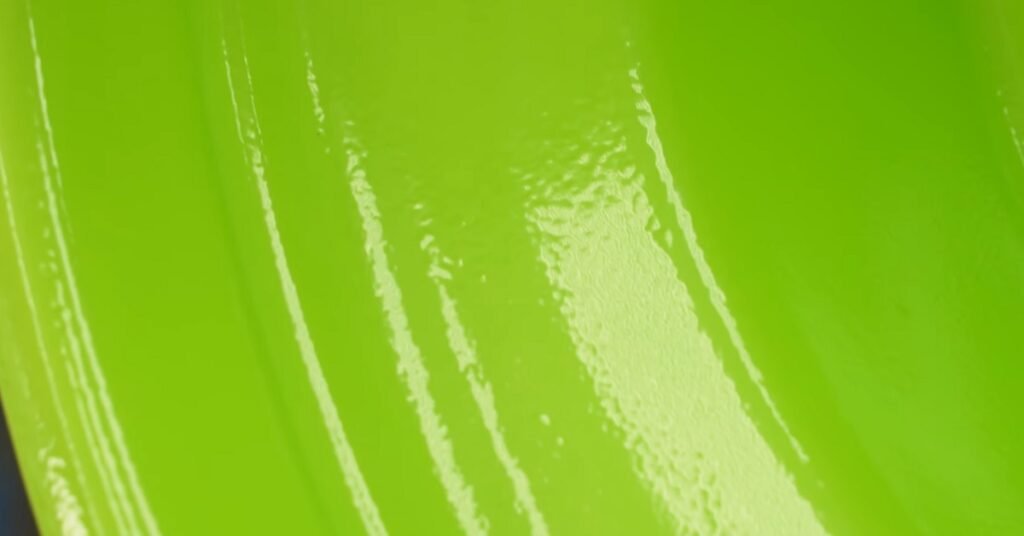
Orange peel is one of the most common and ugly powder coating defects. It leaves the surface with a rough, dimpled texture resembling orange rind. This unsightly defect will diminish the appearance of any finished product.
What Causes Orange Peel?
Orange peel powder coating generally occurs due to issues in the curing process and powder application:
- Incorrect temperature or too little time during curing can inhibit flow and leveling.
- Poor powder flow from the gun caused by bad settings or nozzle blockages.
- Applying too much powder thickness in one coat.
- Insufficient ventilation or air circulation when curing.
Any of these factors can prevent the powder from flowing out smoothly as it cures, resulting in the dimpled, uneven texture.
Solutions for Orange Peel
While ugly, orange peel powder coating can be prevented and corrected by:
- Follow the powder manufacturer’s recommended temperature and duration guidelines precisely during curing. Use sensors to ensure consistency.
- Adjust powder gun settings – pattern, flow rate, voltage, distance – to optimize coverage and flow.
- Apply coats in multiple thinner layers, allowing proper leveling between each layer.
- Ensure adequate fresh air circulation in the curing oven so gasses can dissipate rather than getting trapped in the film.
- For mild cases, gently sand or “knock down” the texture to smooth it out. Severe orange peel may require stripping and re-coating.
Paying careful attention to powder application techniques and the curing process is key to avoiding orange peel texture issues from the start. But even if it occurs, there are ways to smooth it out. Read this in depth guide for preventing orange peel in powder coating.
#4 Fish Eye Defects

Fish eyes manifest as small craters with smooth edges on the coating surface. They are caused by contaminants interfering with powder flow and leveling.
What Causes Fish Eyes?
Typical causes of fish eyes include:
- Oil, silicone or other contaminants present on the surface before coating.
- Contaminants in the powder coating material itself.
- Inadequate mixing or dispersion of fillers and additives in the powder.
Fish eyes must be prevented through cleanliness and proper powder handling.
#5 Blistering Defects
Blistering manifests as bumps or bubbles under the coating surface that can rupture, leaving craters behind. Moisture absorption is the primary cause.
What Causes Blistering?
Blisters mainly form due to:
- Inadequate cleaning leaving contaminants like oil or dirt on the surface.
- Poor surface preparation failing to create proper adhesion.
- Moisture absorption from humidity into the substrate.
- Unsuitable preheating or curing parameters.
Thorough cleaning, pretreatment, and moisture control prevents blistering.
#6 Poor Adhesion
When powder coating doesn’t adhere correctly to the metal surface, it leads to ugly chipping, peeling, and coating failure over time. Proper adhesion is essential for durability.
What Causes Poor Powder Coating Adhesion?
Poor powder coating adhesion often comes down to improper substrate preparation:
- Grease, oil, rust, existing coatings or other contaminants still present on the surface.
- Inadequate abrasion of the surface to support mechanical bonding.
- Mismatch between substrate and coating, resulting in poor chemical bonding.
- Moisture, chromates, or other elements affecting the interface chemistry.
Without proper cleaning, abrasion, and testing, the powder cannot create a tenacious adhesive bond to the metal.
Achieving Excellent Adhesion
To ensure powder coating adheres correctly:
- Media blast or sand substrates to remove coatings/rust and create ideal surface profile.
- Clean meticulously with alkaline baths, phosphating or solvents to eliminate any oils or films.
- Use conversion coatings tailored for the substrate metal to promote chemical bonding.
- Preheat substrates 20°F (11°C) above dew point before coating to prevent moisture reactions.
- Test powder compatibility with the metal using cross-cut or X-hatch adhesion tests before a full production coating run.
Rigorous surface preparation and testing is necessary to guarantee the powder coating adheres correctly for maximum lifespan.
#7 Color Variance Defects
When the color of your powder coated products doesn’t match what is expected, it leads to rejected parts and unhappy customers. Color variance is a problematic but avoidable defect.
What Causes Color Differences in Powder Coating?
The main factors leading to powder coating color variance are:
- Poor mixing of the powder resulting in uneven pigment dispersion throughout the batch.
- Contamination from dirty equipment altering the powder’s properties and reactivity.
- Incorrect powder thickness skewing color perception in certain areas.
- Process drift where application settings shift over time causing inconsistencies.
- Variations in substrate reactivity with the powder chemicals.
From powder preparation to final curing, deviations at each stage of the process can influence the final color achieved.
Achieving Color Consistency
Maintaining strict quality control is the key to achieving consistent powder coating color:
- Use automated mixing equipment to thoroughly blend powders and ensure completely homogeneous pigment distribution.
- Follow stringent cleanliness procedures and prevent any contamination in powder handling and storage areas.
- Apply carefully controlled, uniform powder layer thickness to avoid skewing color perception.
- Closely monitor all application settings to prevent drift or changes over time.
- Test small sample batches first to confirm color match before major production runs.
With rigorous quality control and testing at every stage, you can achieve reliable, consistent colors with your powder coating process.
#8 Cracking and Chipping Defects
Cracking and chipping of the powder coated surface is a common defect indicating problems with film integrity. Even minor cracks quickly lead to corrosion and part failures.
What Causes Cracking and Chipping?
Cracking and chipping defects often result from:
- Excessive coating thickness leading to internal film stresses.
- Over-baking or under-baking resulting in improper powder cure.
- Poor coating selection with inadequate flexibility or impact resistance for the part’s use.
- Preexisting substrate flaws or damage leading to coating stresses.
As the coating expands and contracts during use, these weaknesses cause critical coating failures.
Preventing Cracking and Chipping
Avoiding premature cracks and chips comes down to proper coating application and cure:
- Follow powder manufacturer’s recommended DFT and avoid overly thick coats prone to defects.
- Precisely match the prescribed temperature and duration for curing to prevent under or over-baking.
- Select powder coatings designed for the part’s end use conditions and required impact resistance levels.
- Identify and address any substrate defects through proper pretreatment before applying the powder.
- Consider a lacquer or sealant topcoat for extra protection if the environment will be highly demanding.
Careful attention to thickness, cure schedule, and product selection prevents many coating integrity issues. But proper substrate preparation is also key.
Environmental Factors Affecting Powder Coating Defects
When it comes to achieving a flawless and durable powder coating, it’s not just about the quality of the powder or the skill of the applicator. Environmental factors can play a significant role in the occurrence of defects during the powder coating process.
In this part, we will explore some of the key environmental factors that can impact powder coating and discuss preventive measures to mitigate these defects.
Humidity And Moisture
Humidity and moisture are two major culprits when it comes to powder coating defects. High levels of humidity in the air can interfere with the curing process, causing notable problems such as blistering, bubbling, and poor adhesion. Moisture can also lead to surface contamination, resulting in compromised finish quality.
To prevent humidity-related defects, it is crucial to monitor and control the humidity levels in the coating area. The use of dehumidifiers can help reduce excess moisture in the air, ensuring a more stable coating environment.
Additionally, proper ventilation and air circulation can aid in minimizing the impact of humidity on the powder coating process.
Temperature And Curing
The relationship between temperature and powder coating curing is a delicate one. Extreme temperatures can lead to defects such as wrinkling, orange peel, and insufficient film thickness. On the other hand, insufficient curing temperatures can result in poor adhesion and reduced overall durability.
For optimal powder coating results, it is essential to adhere to the recommended temperature ranges specified by the powder manufacturer. This information can typically be found in the product’s technical data sheet. Maintaining a controlled and consistent curing temperature ensures proper flow and fusion of the powder particles, resulting in a smooth and durable finish.
Dust And Contamination
Dust and contamination can easily find their way onto the surface being coated, causing unsightly defects in the finished product. Sources of dust and contamination can include airborne particles, improper cleaning procedures, and insufficient maintenance of equipment.
To combat these issues, implementing effective contamination control measures is crucial. This can involve the use of cleanrooms or controlled environments, thorough surface cleaning before coating, and regular equipment maintenance.
Proper filtration systems and the use of protective covers can also help minimize the risk of dust and contamination during the coating process.
Operational Errors Leading To Powder Coating Defects
Operational errors during the powder coating process can significantly impact the final quality of the coating. Understanding these errors and their causes is crucial for ensuring a flawless finish.
In this section, we will explore three common operational errors that lead to powder coating defects: improper surface preparation, inadequate powder application, and improper cure times and temperatures.
Improper Surface Preparation
One of the primary causes of powder coating defects is improper surface preparation. The surface must be thoroughly cleaned and pre-treated before the coating is applied. Failure to adhere to proper surface preparation procedures can result in adhesion issues, poor coating thickness, and reduced durability.
The importance of thorough cleaning and pre-treatment cannot be overstated. Before applying the powder, all contaminants such as oil, grease, dirt, and rust must be completely removed from the surface. Proper cleaning techniques include solvent cleaning, sandblasting, or chemical stripping.
By ensuring the surface is clean and free from any impurities, the powder coating can adhere properly and provide maximum protection against corrosion and wear. Thorough surface preparation is a crucial step to achieve a high-quality and long-lasting powder coating finish.
Effects Of Inadequate Surface Preparation On The Coating Quality
Inadequate surface preparation directly impacts the quality of the powder coating. When the surface is not properly cleaned and pre-treated, the powder may not adhere uniformly, leading to inconsistent coating thickness. This can result in patchy appearance, reduced coverage, and uneven color distribution.
Furthermore, contaminants left on the surface can cause the coating to peel or blister over time. Without a clean and properly pre-treated surface, the powder coating’s ability to provide protection against corrosion and wear is compromised, reducing its lifespan and effectiveness.
Inadequate Powder Application
Another common operational error that leads to powder coating defects is inadequate powder application. To achieve a flawless finish, it is essential to understand the proper techniques for applying the powder evenly and uniformly.
When applying the powder, it is crucial to maintain consistent gun speed, gun-to-part distance, and powder flow rate. Deviations from the recommended application parameters can result in uneven or insufficient powder coverage, leading to coating defects such as pinholes, orange peel texture, or poor adhesion.
By following the guidelines for proper powder application, including maintaining the correct gun settings and applying the powder in a controlled environment, manufacturers can achieve a uniform and high-quality coating that meets the desired specifications.
Consequences Of Uneven Or Insufficient Powder Application
The consequences of uneven or insufficient powder application can be detrimental to the coating’s overall quality and performance. In areas with insufficient powder coverage, the underlying substrate may be exposed, making it vulnerable to corrosion and wear.
Uneven coating thickness can result in aesthetic issues, such as color variations and an uneven texture. Moreover, localized thin spots can compromise the coating’s integrity, leading to premature flaking, peeling, or chipping.
To ensure an even and adequate powder application, technicians should undergo proper training and adhere to standardized procedures. With precise control and attention to detail, manufacturers can minimize powder coating defects and achieve a uniform and durable finish.
Improper Cure Times And Temperatures
The cure process plays a vital role in the final quality and performance of the powder coating. Incorrect cure times and temperatures can lead to various coating defects and compromise the coating’s durability and adhesion.
Understanding the optimal cure times and temperatures is essential for achieving a fully cured and robust coating. Manufacturers should follow specific guidelines, provided by the powder manufacturer, which typically include recommended cure temperatures and dwell times.
Deviation from the recommended cure parameters can result in under-cured or over-cured coatings. Under-curing can lead to poor adhesion and reduced mechanical strength, while over-curing can cause discoloration, brittleness, and reduced chemical resistance.
By diligently following the guidelines for cure times and temperatures, manufacturers can ensure the powder coating is properly cured, maximizing its protective qualities and ensuring long-term performance.
How to Prevent Powder Coating Defects
Powder coating defects can be frustrating and costly, but with the right strategies and quality control measures, they can be minimized and even prevented. By implementing the following strategies and maintaining regular inspections, you can ensure that your powder coated products meet the highest standards of quality.
Strategies For Preventing And Minimizing Powder Coating Defects
To overcome powder coating defects, it’s important to establish a solid foundation by implementing proven preventive strategies. By taking proactive measures, you can significantly reduce the risk of defects and ensure a flawless finish:
Surface Preparation
Properly prepare the substrate by cleaning, degreasing, and removing any contaminants that may interfere with the adhesion of the powder.
Powder Application Techniques
Apply a consistent and even coat of powder by using appropriate application techniques such as electrostatic spray or fluidized bed coating.
Curing Process
Follow the manufacturer’s specifications for the curing process, including the correct temperature and duration. Avoid over-curing or under-curing the powder, as this can lead to defects.
Equipment Maintenance
Regularly inspect and maintain your powder coating equipment to ensure it is functioning optimally. Clean filters, check gun settings, and replace worn parts to prevent defects caused by equipment malfunction.
Training and Skill Development
Invest in training your powder coating technicians to improve their skills and knowledge. Proper training can help them identify potential defects and take corrective actions promptly.
Importance Of Regular Inspection And Quality Control Measures
Regular inspection and quality control measures are crucial in identifying and addressing any powder coating defects before they become widespread. By implementing these measures, you can ensure that your products meet the highest standards of quality, reduce rework and rejection rates, and maintain customer satisfaction:
Visual Inspection
Conduct thorough visual inspections to identify defects such as coating thickness variations, orange peel, bubbles, fisheyes, or other imperfections. Train your inspectors to recognize these defects and take appropriate actions.
Adhesion and Hardness Testing
Perform adhesion and hardness tests to ensure that the powder coating is properly bonded to the substrate and has the required hardness for its intended use.
Destructive Testing
Occasionally perform destructive tests to assess the coating’s resistance to impact, corrosion, and other stress factors. This will help identify any defects that may not be apparent during visual inspections alone.
Documentation and Record Keeping
Maintain detailed records of inspections, test results, and any corrective actions taken. This documentation will enable you to track defect trends, identify areas for improvement, and demonstrate compliance with industry standards.
Continuous Improvement
Regularly review your quality control processes, analyze defect data, and implement improvements. By continuously striving for improvement, you can prevent future defects and optimize your powder coating operations.
By implementing these preventive strategies and embracing regular inspections and quality control measures, you can overcome powder coating defects and deliver superior products to your customers.
Remember, prevention is always better than dealing with costly rework or dissatisfied customers. Invest in robust processes, training, and equipment maintenance to ensure the success of your powder coating operations.
Frequently Asked Questions For Powder Coating Defects And Causes
What Are The Defects Of Coating Failure?
The defects of coating failure include peeling, blistering, cracking, delamination, and discoloration.
What Causes Coating Imperfections?
Coating imperfections result from various factors, such as inadequate surface preparation, improper application techniques, or substandard coating materials.
How Do You Fix Imperfections In Powder Coating?
To fix imperfections in powder coating, follow these steps:
- 1. Clean the surface thoroughly.
- 2. Sand down any rough spots or bubbles.
- 3. Apply a new coat of powder using an even, smooth technique.
- 4. Bake the coated object in an oven according to manufacturer’s instructions.
- 5. Inspect the final result for any remaining imperfections.
What Is The Sagging Defect In Powder Coating?
Sagging is a defect in powder coating where the coating appears to sag or droop on the surface. It can occur due to excessive coating thickness, improper curing, or inadequate pre-treatment. Sagging can result in an uneven and unattractive finish.
Final Thoughts
Defects in powder coating can undermine the finish’s appearance and protective properties when overlooked. By understanding common issues like orange peel, poor adhesion, pinholes, color variance, and cracking, proactive steps can be taken to avoid them.
Proper pretreatment, powder application, curing methods, and preventive maintenance are essential for flawless results. While powder coating offers many benefits, it requires diligent process control and testing to minimize risks for defects.
Implementing the solutions outlined here will help elevate your powder coating operation and reduce headaches from continual defects. With attention to detail and process refinement, achieving beautiful, durable powder coated finishes can become routine.