Orange peel in powder coating refers to the texture or surface irregularities that resemble the skin of an orange. It occurs due to improper application or curing process, leading to a rough, bumpy finish that compromises the visual appearance and quality of the coated surface.
When it comes to achieving a flawless and professional finish in powder coating, the presence of orange peel can be frustrating. Orange peel refers to the textured appearance on the surface of a powder-coated object that resembles the peel of an orange. Understanding the causes of orange peel is crucial in order to prevent it and achieve a smooth, high-quality finish.
In this article, we will delve into the various factors that contribute to orange peel in powder coating.
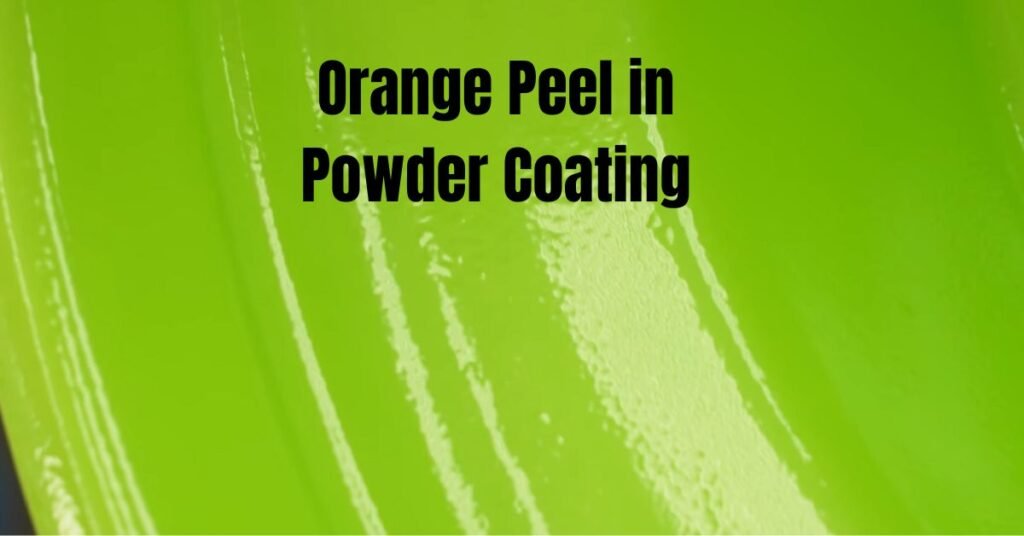
What Is Orange Peel In Powder Coating?
Orange peel refers to a bumpy, dimpled, or uneven texture that arises on powder coated surfaces. It can range from a fine texture to large, visible bumps that significantly degrade the appearance. This irregular texture resembles the exterior of an orange’s peel, hence the name.
While it may seem like just a superficial issue, orange peel can also negatively impact the coating’s protective performance and longevity. The bumps and valleys on the surface make it harder to clean and maintain. They also provide crevices for contaminants and corrosion to take hold, disrupting the protective properties of the coating.
Causes Of Orange Peel In Powder Coating
1. Incorrect Powder Coating Technique
The application technique plays a crucial role in the formation of orange peel. If the powder coating is applied too thickly or unevenly, it can result in an uneven texture on the surface. Additionally, improper curing or incorrect temperature settings during the curing process can also contribute to the development of orange peel.
2. Inadequate Equipment Calibration
The equipment used for powder coating, such as spray guns and curing ovens, must be properly calibrated in order to achieve a smooth finish. Inadequate calibration can lead to inconsistent powder application, resulting in orange peel. Regular maintenance and calibration of the equipment are essential to avoid this issue.
3. Improper Surface Preparation
Before applying the powder coating, proper surface preparation is crucial to ensure adhesion and a smooth finish. If the surface is not adequately cleaned, degreased, or properly pretreated, it can lead to orange peel. Contaminants or imperfections on the surface can interfere with the powder coating process, resulting in a textured appearance.
4. Environmental Factors
The surrounding environment can also contribute to the formation of orange peel. Factors such as high humidity, temperature variations, or insufficient ventilation can affect the application and curing process, leading to the development of orange peel.
5. Powder Coating Material Related Issues
The quality and composition of the powder coating material can impact the final finish. Issues such as the incorrect powder-to-resin ratio, poor flow characteristics, or inadequate powder particle size can result in orange peel. It is essential to select high-quality powder coating materials and ensure proper mixing and preparation.
We hope now you understanding the causes of orange peel in powder coating, you can take the necessary steps to prevent this issue and achieve a flawless finish. Proper technique, equipment calibration, surface preparation, consideration of environmental factors, and using high-quality materials all contribute to a successful powder coating process.
Effects Of Orange Peel On Powder Coated Surfaces
Orange peel is a common issue that can affect the quality and appearance of powder coated surfaces. It refers to the texture that resembles the skin of an orange, characterized by a bumpy or uneven surface. Orange peel occurs during the powder coating process when the coating is not evenly applied or when the curing process is not executed properly. While orange peel may seem like a minor aesthetic concern, it can have significant impacts on both the appearance and performance of the powder coated surface.
Visual Impact
The bumpy, wavy appearance of orange peel is visually unappealing and looks unprofessional. It interferes with the desired uniform, smooth finish of powder coating. This aesthetic damage reduces the perceived quality and value of the product or surface.
For applications where looks are paramount, like in automotive finishing or consumer goods, orange peel can render the finish unacceptable, resulting in reworking or rejection. It negatively impacts business costs and brand reputation.
Functional Impairment
Beyond just visual flaws, the texture caused by orange peel also impairs the protective capabilities of the coating, decreasing durability and longevity:
- Difficulty in cleaning – The rough texture accumulates and traps dirt, grease, oils and other contaminants. It prevents easy cleaning and maintenance.
- Reduced corrosion resistance – Crevices in the uneven surface allow moisture, oxygen, and chemicals to penetrate the coating and attack the substrate. This leads to corrosion, compromising protection.
- Decreased coating integrity – Bumps and valleys place stresses on the coating film, making it prone to damage from impact, scratching, UV exposure, and other threats.
By understanding the range of detrimental effects orange peel can have on performance and aesthetics, businesses can better appreciate the value of implementing preventive measures and quality control processes.
Preventing Orange Peel In Powder Coating
When it comes to powder coating, achieving a smooth, blemish-free finish is crucial. One common issue that can arise during the powder coating process is orange peel. Orange peel refers to a textured, dimpled appearance on the coated surface, resembling the skin of an orange. This can be a frustrating problem, as it compromises the overall aesthetics and quality of the finished product. Fortunately, there are various techniques and factors that can help prevent orange peel in powder coating.
We will explore some key considerations and best practices to ensure a flawless powder coating finish.
1. Proper Powder Coating Technique
The first step in preventing orange peel is to ensure that the powder coating technique is carried out correctly. This involves following industry best practices and adhering to recommended guidelines. It is essential to have a thorough understanding of the equipment, materials, and processes involved in powder coating. Proper technique includes factors such as proper gun-to-part distance, appropriate powder coating thickness, controlled powder film flow, equipment calibration, and gun settings adjustment.
2. Correct Powder Application
Applying the powder correctly is crucial to achieving a smooth finish. The powder should be evenly and uniformly applied on the surface. Proper application techniques, such as using an appropriate gun-to-part angle and maintaining a consistent powder flow, can help prevent orange peel. It is also essential to consider factors like the type of powder being used and the specific characteristics of the surface being coated.
3. Optimal Oven Cure Schedule
The curing process plays a significant role in preventing orange peel. The oven cure schedule must be carefully calculated to ensure that the powder cures properly without causing undesirable surface textures. Factors such as temperature and curing time should be determined based on the type of powder, substrate, and desired finish. A controlled cure schedule is essential to avoid over-baking or under-baking the powder, which can lead to orange peel and other defects.
4. Suitable Gun-to-part Distance
Proper gun-to-part distance is critical for achieving an even and consistent coating. If the gun-to-part distance is too close, excessive powder can be deposited, resulting in orange peel. On the other hand, if the distance is too far, insufficient coverage may occur, causing patchiness or uneven coating. It is important to maintain an optimal gun-to-part distance throughout the application process for a smooth finish.
5. Appropriate Powder Coating Thickness
The thickness of the powder coating layer also plays a role in preventing orange peel. A coating that is too thin may not fully flow and level, resulting in a textured appearance. Conversely, an excessively thick coating can lead to orange peel due to uneven powder flow and curing. It is crucial to follow the recommended coating thickness guidelines to achieve a flawless finish.
6. Controlled Powder Film Flow
The flow of powder during application is a critical factor in preventing orange peel. Controlling the powder film flow ensures that the coating is evenly distributed, with no excess or patchiness. Techniques such as adjusting the powder flow rate, using appropriate gun settings, and maintaining consistent air pressure can help achieve optimal powder film flow and minimize orange peel.
7. Equipment Calibration
Regular calibration of powder coating equipment is necessary to ensure accurate and consistent application. This includes calibrating the equipment settings, such as the gun, air pressure, and powder flow, to achieve the desired coating quality. Proper calibration helps maintain a controlled and precise powder application, minimizing the risk of orange peel and other defects.
8. Gun Settings Adjustment
The gun settings, including the spray tips, electrostatic charge, and air pressure, should be adjusted correctly to prevent orange peel. The spray pattern should be fine and even, ensuring that the powder is uniformly distributed on the surface. The electrostatic charge and air pressure should be adjusted according to the specific powder and substrate, enabling proper adhesion and flow.
9. Gun-to-part Angle Considerations
Choosing the appropriate gun-to-part angle during powder coating is essential to achieve a smooth finish. The angle at which the gun is held relative to the surface affects the powder distribution and flow. Finding the optimal angle based on the shape and contours of the part helps ensure uniform coverage without orange peel. It may be necessary to adjust the angle during the application process to maintain consistent coating quality.
10. Regular Maintenance And Cleaning
Maintaining and cleaning the powder coating equipment regularly is crucial for preventing orange peel. Accumulated dirt, debris, or powder residue can interfere with the coating process and result in defects. Regular cleaning of the equipment, including the gun, spray booth, filters, and nozzles, helps maintain optimal performance and ensures a smooth, flawless finish.
11. Surface Preparation Techniques
Proper surface preparation is critical for achieving a high-quality powder coating and preventing orange peel. This involves cleaning and degreasing the surface, roughening the surface to enhance adhesion, and managing environmental factors that can affect the coating process.
12. Cleaning And Degreasing
Prior to powder coating, the surface must be thoroughly cleaned and degreased to remove any contaminants that could impair adhesion. Proper cleaning methods, suitable detergents, and appropriate degreasing agents should be used to ensure a clean and residue-free surface.
13. Surface Roughening Methods
Roughening the surface helps improve the bond between the powder coating and the substrate, reducing the likelihood of orange peel. Techniques such as abrasion or the use of chemical etchants can be employed to create a suitable surface profile for enhanced adhesion.
14. Preheating And Vapor Degreasing
In certain cases, preheating the substrate or using vapor degreasing methods can be advantageous to eliminate moisture, oils, and other contaminants that can cause orange peel. These methods should be used judiciously, considering the specific requirements of the substrate and the powder coating process.
15. Managing Environmental Factors
Controlling environmental factors during powder coating is crucial for achieving a smooth, defect-free finish. Factors such as temperature, humidity, dust, and contaminants can significantly impact the coating process and increase the likelihood of orange peel or other defects.
16. Temperature And Humidity Control
Maintaining appropriate temperature and humidity levels in the powder coating environment is essential for ensuring optimal coating quality. Extreme temperatures or high humidity can affect the powder flow, curing process, and overall coating appearance. Proper temperature and humidity control help minimize the risk of orange peel.
17. Dust And Contaminant Prevention Measures
A clean and dust-free environment is crucial for achieving a flawless powder coating. Implementing measures such as proper ventilation, air filtration, and dust control methods helps minimize the presence of contaminants that can cause defects like orange peel.
18. Adequate Ventilation
Proper ventilation in the powder coating area is essential for removing airborne contaminants and maintaining a clean workspace. It helps prevent the accumulation of overspray, dust particles, or other impurities that could affect the coating quality, resulting in orange peel.
19. Proper Selection And Handling Of Powder Coating Materials
Choosing the right powder coating materials and handling them appropriately is crucial for preventing orange peel. Proper storage, handling, and mixing of powders help maintain their integrity and ensure consistent coating quality. It is important to follow the manufacturer’s guidelines and recommended procedures for handling various types of powder coatings.
20. Powder Quality Evaluation
Evaluating the quality of the powder coating material is essential to prevent defects like orange peel. Visual inspection, particle size analysis, and other quality control measures can help identify any irregularities in the powder that may affect the finish. Using high-quality powders with consistent properties reduces the risk of orange peel and ensures a smooth, uniform coating.
21. Proper Storage And Handling Practices
Proper storage and handling of powder coatings are vital to maintain their quality and prevent issues like orange peel. Powders should be stored in a controlled environment, away from moisture, extreme temperatures, and contaminants. Following recommended storage and handling practices helps preserve the integrity of the powder and ensures consistent coating results.
How Identifying The Orange Peel
There are several steps that can be taken to identify the cause of orange peel. Visual inspection techniques play a vital role in this process, allowing you to analyze the affected surface for any abnormalities or imperfections. By closely examining the coating, you can determine if the orange peel effect is caused by issues such as improper surface preparation, equipment calibration problems, or environmental factors.
Visual Inspection Techniques
Visual inspection techniques involve carefully examining the powder coated surface to identify the root cause of orange peel. By using proper lighting and magnification tools, you can closely observe the texture, thickness, and uniformity of the coating. Look for any signs of contamination, unevenness, or inconsistent gloss levels. These visual cues provide valuable insights into the factors contributing to orange peel and help guide corrective actions.
Quality Control Measures
Integrating quality control measures throughout the powder coating process is essential for resolving orange peel issues. This includes regularly monitoring and documenting key parameters such as the powder thickness, curing temperature, and dwell time. By implementing a comprehensive quality control system, you can identify any deviations from desired specifications and take proactive measures to rectify them, minimizing the occurrence of orange peel.
Short Fixing Of Orange Peel
Fixing orange peel requires targeted corrective actions based on the identified cause. Several common causes can lead to this issue, such as improper technique variables, equipment calibration problems, surface preparation inadequacies, and environmental factors. Here are some possible corrective actions:
Cause | Corrective Action |
---|---|
Improper technique variables | Adjust powder flow rate, gun settings, or voltage |
Equipment calibration problems | Calibrate and maintain equipment regularly |
Surface preparation inadequacies | Redo or enhance surface preparation before coating |
Environmental factors | Manage temperature, humidity, and airflow effectively |
Adjusting Powder Coating Technique Variables
One of the most effective ways to fix orange peel is by adjusting various technique variables during the powder coating process. This includes modifying the powder flow rate, gun settings, or voltage to achieve optimal coating uniformity. By fine-tuning these variables based on the specific requirements of your project, you can significantly reduce or eliminate the occurrence of orange peel.
Calibration And Maintenance Of Equipment
Proper calibration and regular maintenance of powder coating equipment are essential for achieving consistent and high-quality results. By periodically calibrating the equipment, you can ensure accurate powder and airflow control, preventing issues like orange peel. Additionally, regular maintenance, including cleaning and replacing worn-out parts, helps maintain equipment efficiency and prolong its lifespan.
Surface Preparation Redo Or Enhancement
The surface preparation process significantly impacts the quality of the powder coated finish. If orange peel is a recurring issue, it may be necessary to redo or enhance the surface preparation steps. Thoroughly cleaning the substrate, removing any contaminants, and applying suitable treatments like primers or etching solutions can improve the adhesion and overall quality of the powder coating, addressing the orange peel problem.
Managing Environmental Factors
Environmental factors, such as temperature, humidity, and airflow, can have a significant impact on the quality of the powder coating. By effectively managing these variables, you can minimize the occurrence of orange peel. Controlling the temperature and humidity within the recommended range and ensuring proper airflow in the coating booth or oven can contribute to a more consistent and smoother coating application.
Powder Coating Material Reevaluation
Reevaluating the powder coating material itself is another important step in resolving orange peel issues. It is crucial to ensure that the powder is of high quality and suitable for the specific application. Consider factors such as the powder particle size distribution, resin formulation, and curing characteristics. Sometimes, changing to a different powder coating material can eliminate orange peel problems.
Most Affective Way to Avoid Orange Peel in Powder Coating?

As experienced powder coating technicians, we want to share the most effective way we’ve found to avoid orange peel.
The key is using less powder than you’d think necessary. It’s tempting for us to apply heavy coats, but restraint is crucial. We need to use just enough powder to lightly cover the surface – no more.
Also, it’s best if we handle parts as little as possible during powder coating. The more we touch the part, the more likely powder clumps and unevenness can occur.
Finally, we recommend using a voltage on the lower end of the recommended range. Higher voltages speed up curing, which can trap imperfections in the powder surface.
By following these three simple powder coating best practices that we stand by, we’ll achieve smooth, glossy finishes free of orange peel texture:
- Light on powder
- Light on handling
- Low voltage
We’ve used this precise technique to powder coat hundreds of parts flawlessly. Trust us, less is more when it comes to avoiding orange peel.
Final Thoughts
Understanding and addressing the issue of orange peel in powder coating is essential for achieving a flawless finish. By recognizing the causes, such as improper application techniques or inadequate curing time, manufacturers can take proactive steps to eliminate orange peel and deliver high-quality products.
By prioritizing thorough preparation and following industry best practices, companies can enhance the durability and aesthetics of their powder coating applications, leading to increased customer satisfaction and business success.