If you’ve ever considered protecting your metal products, you’ve likely come across powder coating as a popular method. But what if I told you there are alternatives that can deliver excellent results and may even be more suitable for your specific needs? In this article, we’ll delve into the world of powder coating alternatives, exploring the pros and cons of each to help you make an informed decision.
The Evolution of Powder Coating
Before we jump into alternatives, let’s briefly understand what powder coating is and why you might be seeking alternatives. Powder coating is a technique that involves applying a dry powder to a surface and then curing it with heat. It’s known for its durability, attractive finish, and environmental benefits. However, it may not always be the best choice for every situation.
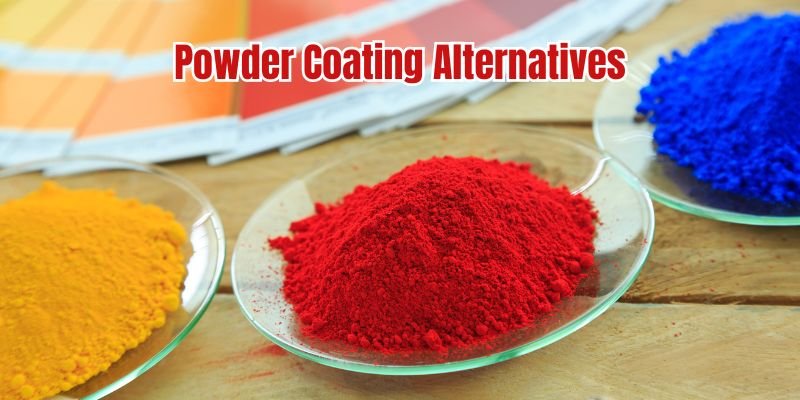
Powder Coating Alternatives: An Overview
The Need for Alternatives
With traditional powder coating methods, some limitations have become apparent. These include concerns about environmental impact, cost, and versatility. Fortunately, innovative alternatives are emerging to address these issues, ensuring a more sustainable future.
An Eco-Friendly Approach
Today, the demand for environmentally friendly solutions is on the rise. Many alternative coating methods offer reduced environmental impact, making them a conscious choice for both manufacturers and consumers.
Economic Benefits
In addition to environmental considerations, cost-effectiveness plays a significant role in the selection of a coating method. We’ll explore how these alternatives can save you money while maintaining quality.
Now, Exploring the World of Alternatives
Exploring Liquid Coating As An Alternative
When it comes to coating options, powder coating has long been a popular choice due to its durability and versatility. However, there is an alternative that offers its own set of advantages – liquid coating. In this section, we will dive into the world of liquid coating, understanding its properties, benefits, and popular types.
Understanding liquid coating
Liquid coating is a type of coating that is applied as a liquid and then dries into a protective film. Unlike powder coating, which is applied using an electrical charge and heat, liquid coating is typically applied using a spray gun or roller. This allows for easy application on various surfaces, including metal, plastic, and wood.
Benefits of liquid coating over powder coating
While powder coating has its advantages, liquid coating offers a range of benefits that may make it a more suitable option for certain projects. Here are some key advantages of liquid coating:
- Greater color options: Liquid coatings offer a wider range of color options compared to powder coatings. This allows for greater customization and the ability to match specific color requirements.
- Thinner coating: Liquid coatings can be applied in a thinner layer compared to powder coatings. This can result in a more even and smooth finish, especially on intricate or delicate surfaces.
- Better UV resistance: Liquid coatings often provide better UV resistance, making them ideal for outdoor applications that are exposed to sunlight. This helps prevent fading, discoloration, and damage caused by UV rays.
- Easy touch-up: Liquid coatings are easier to repair or touch-up compared to powder coatings. If a spot of coating gets chipped or damaged, it can be easily re-applied without the need for extensive surface preparation.
Popular types of liquid coatings
There are several types of liquid coatings available, each with its own unique properties and applications. Here are some popular types:
Type of Liquid Coating | Features and Applications |
---|---|
Epoxy | Provides excellent adhesion and corrosion resistance. Commonly used for industrial purposes, such as metal equipment and pipes. |
Polyurethane | Offers high durability and chemical resistance. Ideal for surfaces that require protection against abrasion, chemicals, and moisture. |
Acrylic | Provides a durable, glossy finish. Often used for automotive coatings, furniture, and decorative applications. |
Alkyd | Offers good color retention and weather resistance. Commonly used for outdoor applications, such as metal fences and railings. |
These are just a few examples of the wide variety of liquid coatings available. The right type of coating will depend on the specific requirements of your project.
Considerations for Liquid Coating
- Drying Time: Liquid coatings usually require more time to dry than powder coatings.
- Environmental Impact: Some liquid coatings may contain volatile organic compounds (VOCs), which can harm the environment.
Electrostatic Spray Painting: A Viable Alternative
When it comes to coating surfaces, powder coating has long been the go-to choice for industries and individuals alike. However, there are alternative methods that can achieve similar results with their own unique advantages. One such alternative is electrostatic spray painting. In this article, we will take a closer look at electrostatic spray painting, how it differs from powder coating, and explore its advantages and disadvantages. Let’s dive in!
Introduction to electrostatic spray painting
Electrostatic spray painting is a technique that involves the application of a thin, even layer of paint or coating onto a surface using an electrostatic charge. Unlike powder coating, which involves applying dry powder and then curing it with heat, electrostatic spray painting uses a liquid paint or coating.
Through the use of specialized equipment, the liquid paint is atomized into tiny droplets and given a positive charge. The surface to be coated is grounded or given a negative charge. As the charged droplets are sprayed towards the surface, they are attracted to it, creating an even and smooth coating that adheres well.
How it differs from powder coating
While both electrostatic spray painting and powder coating are effective coating methods, there are a few key differences between them.
Firstly, as mentioned earlier, the major difference lies in the state of the material being applied. Electrostatic spray painting uses liquid paint, while powder coating utilizes dry powder. This distinction affects the application process as well as the final result. Powder coating requires a curing process that typically involves heat, whereas electrostatic spray painting does not.
Secondly, the nature of the coating achieved also differs between the two methods. Powder coating usually results in a thicker and more durable coating, making it suitable for applications that require high resistance to abrasion and corrosion. On the other hand, electrostatic spray painting tends to produce a thinner and more lightweight coating, which can be advantageous in certain situations where weight or flexibility is a concern.
Advantages and disadvantages of electrostatic spray painting
Like any coating method, electrostatic spray painting comes with its own set of pros and cons. Let’s take a look at some of the advantages and disadvantages of this technique.
Advantages | Disadvantages |
---|---|
|
|
Electrostatic spray painting presents a viable alternative to powder coating for certain applications. Its ability to achieve smooth finishes, use a variety of coatings, and offer customization options make it a suitable choice for projects where durability is not the primary concern.
However, it’s essential to consider the specific requirements of your project and assess whether electrostatic spray painting meets your needs. With proper understanding and application, electrostatic spray painting can be a valuable tool in the coating industry.
Dipping And Immersion Coating: Effective Alternatives
When it comes to coating methods, many people are familiar with powder coating. However, it’s important to note that there are alternative options available, such as dipping and immersion coating. We will explore what dipping and immersion coating is, how they compare to powder coating, and the key benefits and applications of these alternative methods.
What is dipping and immersion coating?
Dipping and immersion coating are methods of applying a protective or decorative finish to various objects. These processes involve submerging the object into a liquid coating material, allowing it to fully cover the surface before being removed and cured, resulting in a durable and uniform coating.
How dipping and immersion coating compare to powder coating?
In comparison to powder coating, dipping and immersion coating offer unique advantages for specific applications. While powder coating involves the electrostatic application of dry powder onto the object’s surface, dipping and immersion coating allow for a more complete and even coverage. This makes it ideal for coating three-dimensional objects with complex shapes or intricate designs.
Key benefits and applications of dipping and immersion coating
Dipping and immersion coating offer several key benefits that make them effective alternatives to powder coating. Some notable advantages include:
- Uniform Coverage: The immersion process ensures that the entire object is evenly coated, including hard-to-reach areas and corners.
- Improved Durability: The immersion coating creates a strong bond between the object and the coating material, resulting in enhanced durability and resistance to wear and tear.
- Wide Variety of Coating Materials: Dipping and immersion coating can be performed with different types of coating materials, including paints, varnishes, enamels, and more, allowing for customization and versatility.
- Time and Cost Efficiency: These methods generally require less equipment, energy, and maintenance, making them more cost-effective and time-efficient compared to powder coating.
These benefits make dipping and immersion coating suitable for various applications, including:
- Automotive industry for coating car parts
- Marine industry for coating boat and ship components
- Industrial equipment for corrosion protection
- Decorative finishes for furniture and home decor
In conclusion, while powder coating is a popular and effective method, dipping and immersion coating provide viable alternatives with their own set of advantages. Whether you need uniform coverage, improved durability, or a wide variety of coating materials, consider exploring dipping and immersion coating for your next project.
Thermoplastic And Thermosetting Coating: Innovative Alternatives
When it comes to protecting and enhancing the longevity of various surfaces, powder coating has established itself as a reliable and efficient solution. However, there are innovative alternatives to powder coating as well. Two prominent options that have gained traction in recent years are thermoplastic and thermosetting coatings. These coatings offer unique benefits and are widely utilized across several industries.
Differentiating Thermoplastic and Thermosetting Coatings
Understanding the differences between thermoplastic and thermosetting coatings is essential when considering which option best suits a specific application. Both coatings are applied using heat, but they differ in their behavior and performance attributes.
A thermoplastic coating is characterized by its ability to soften and melt when heated, allowing for easy reapplication or removal. This property is particularly advantageous as it enables the coating to be reshaped and reworked without detrimental effects. Additionally, thermoplastic coatings have excellent chemical resistance, making them suitable for environments where corrosion or chemical exposure is a concern.
On the other hand, a thermosetting coating undergoes a chemical reaction when heated, resulting in a permanent cross-linked structure. Once it cures, it cannot be softened or re-melted, making it highly durable and resistant to solvents and chemicals. Thermosetting coatings also offer superior mechanical strength and are known for their excellent adhesion properties.
Benefits and Limitations of Thermoplastic and Thermosetting Coatings
Both thermoplastic and thermosetting coatings have their own set of advantages and limitations. Understanding these factors is crucial for choosing the right coating option.
Thermoplastic Coatings | Thermosetting Coatings |
---|---|
|
|
Prominent Industries Using These Coating Alternatives
Both thermoplastic and thermosetting coatings have found extensive applications across various industries. Here are some prominent sectors utilizing these coating alternatives:
- Automotive Industry: Many automotive components require durable and chemical-resistant coatings for protection against corrosion and wear.
- Electronics Industry: Thermoplastic and thermosetting coatings are widely utilized for circuit boards and electronic components, providing insulation and protection against environmental factors.
- Industrial Machinery and Equipment: Coatings are indispensable for machinery parts and equipment, ensuring optimal performance and protection against harsh environments.
- Furniture and Appliances: Thermoplastic and thermosetting coatings enhance the aesthetics, durability, and longevity of furniture, appliances, and fixtures.
- Sports and Recreation: The sports industry often employs these coatings for various equipment and accessories, ensuring resistance to wear, impact, and weathering.
Thermoplastic and thermosetting coatings offer innovative alternatives to powder coating, each with its own unique characteristics and advantages. Understanding their differences, benefits, and limitations allows industries to make informed decisions when selecting the most suitable coating option for their specific requirements.
Electrocoating: Immersing in Excellence
Electrocoating, also known as e-coating or electrophoretic deposition, is another intriguing alternative to powder coating. This method involves immersing the object in a tank filled with paint and applying an electrical charge to attract the paint particles.
Advantages of Electrocoating
- Uniform Coating: Electrocoating ensures even coverage, even in recessed or complex shapes.
- Corrosion Resistance: This method provides exceptional protection against corrosion.
- Cost-Effective: It minimizes paint wastage, making it a cost-efficient choice.
Considerations for Electrocoating
- Limited Color Variety: Electrocoating is often limited in color options compared to liquid coatings.
- Initial Setup: The equipment and setup costs for electrocoating can be relatively high.
Anodizing: The Aluminum Alchemy
Anodizing is a specialized technique primarily used on aluminum surfaces. It involves creating an oxide layer on the metal’s surface, which provides enhanced durability and corrosion resistance.
Advantages of Anodizing
- Exceptional Durability: Anodized surfaces are incredibly tough and resistant to wear and tear.
- Unique Aesthetic: Anodizing can produce striking metallic finishes that are hard to replicate with other methods.
- Environmental Friendliness: Anodizing is an eco-friendly process that produces minimal waste.
Considerations for Anodizing
- Limited Applicability: Anodizing is primarily suited for aluminum, making it less versatile than some other options.
- Color Limitations: The color choices in anodizing are somewhat limited, and custom colors may not be achievable.
Galvanizing: Rust-Resistant Armor
Galvanizing is a corrosion protection method that involves applying a layer of zinc to a metal surface. This process creates a barrier against moisture and air, effectively preventing corrosion.
Advantages of Galvanizing
- Superb Corrosion Resistance: Galvanized surfaces are highly resistant to rust and corrosion.
- Longevity: Galvanized coatings have a long lifespan, reducing the need for frequent reapplication.
- Low Maintenance: Once galvanized, a surface requires minimal maintenance to stay protected.
Considerations for Galvanizing
- Aesthetic Appeal: Galvanizing does not offer the same aesthetic flexibility as powder or liquid coatings.
- Limited Applicability: It is mainly used for steel and iron surfaces.
Ceramic Coating: Cutting-Edge Technology
Ceramic coating is a relatively new and innovative alternative to traditional coatings. It involves applying a liquid polymer infused with ceramic particles to the surface, creating an extremely durable and protective layer.
Advantages of Ceramic Coating
- Unmatched Durability: Ceramic coatings can last for years, providing superb protection.
- Enhanced Aesthetics: They offer a glossy, showroom-quality finish.
- Hydrophobic Properties: Ceramic coatings repel water and contaminants, keeping surfaces cleaner.
Considerations for Ceramic Coating
- Cost: Ceramic coatings can be more expensive than traditional methods.
- Professional Application: Achieving the best results often requires professional application.
Choosing the Right Alternative
Selecting the ideal coating method depends on various factors, including the material, intended use, budget, and desired aesthetics. Here are some key considerations to help you make an informed choice:
1. Material Compatibility
Consider the type of material you’re coating. For instance, if you’re dealing with aluminum, anodizing might be your best choice. If it’s steel or iron, galvanizing could be more suitable.
2. Aesthetics
Think about the visual appeal you want to achieve. Liquid coatings offer a broad range of colors, while ceramic coatings provide a glossy finish. Choose the option that aligns with your aesthetic goals.
3. Durability
Evaluate the expected wear and tear on the coated surface. If you need maximum durability, consider options like galvanizing or ceramic coatings.
4. Environmental Impact
If sustainability is a concern, look into the environmental impact of your chosen coating method. Powder and anodizing tend to be more eco-friendly.
FAQs:
What Are Some Alternatives To Powder Coating?
There are several alternatives to powder coating, including liquid painting, electrocoating, and anodizing. Each method has its advantages and disadvantages, so it’s important to consider factors such as cost, durability, and environmental impact when choosing the right alternative for your application.
Is Powder Coating The Best Option For Every Project?
While powder coating is a popular choice for many projects, it may not be the best option in every case. Factors such as the material being coated, the desired finish, and the application method can all impact the effectiveness of powder coating.
It’s always a good idea to consult with a professional to determine the best coating option for your specific project.
What Are The Advantages Of Powder Coating?
Powder coating offers several advantages over other coating methods. It provides a durable finish that is resistant to chipping, scratching, and fading. It also offers a wide range of color options and is environmentally friendly, as it does not contain harmful solvents.
Additionally, powder coating is a cost-effective option for large-volume projects.
Are There Any Downsides To Powder Coating?
While powder coating has many advantages, it does have a few downsides to consider. It requires special equipment and facilities for application, which can be a barrier for smaller projects. Powder coating is also limited in its ability to achieve thin or intricate coatings, and it may not be as resistant to certain chemicals or extreme weather conditions as other coating methods.
Final Thoughts
Powder coating may be the go-to option for many applications, but it’s not the only one. Depending on your specific needs, you might find that liquid coating, electrocoating, anodizing, galvanizing, or ceramic coating better suit your project. Each of these alternatives has its own set of advantages and considerations, so it’s essential to weigh them carefully before making a decision.
Remember, the right choice can significantly impact the longevity, appearance, and overall performance of your coated items. So, explore the possibilities and make an informed decision to ensure your project shines with the perfect finish.