Powder coating is a versatile and efficient way to provide a durable and attractive finish to various surfaces. To master this craft, understanding the intricacies of powder coating temperature and time is crucial. In this comprehensive guide, we’ll explore the importance of these factors, providing you with valuable insights and expert advice.
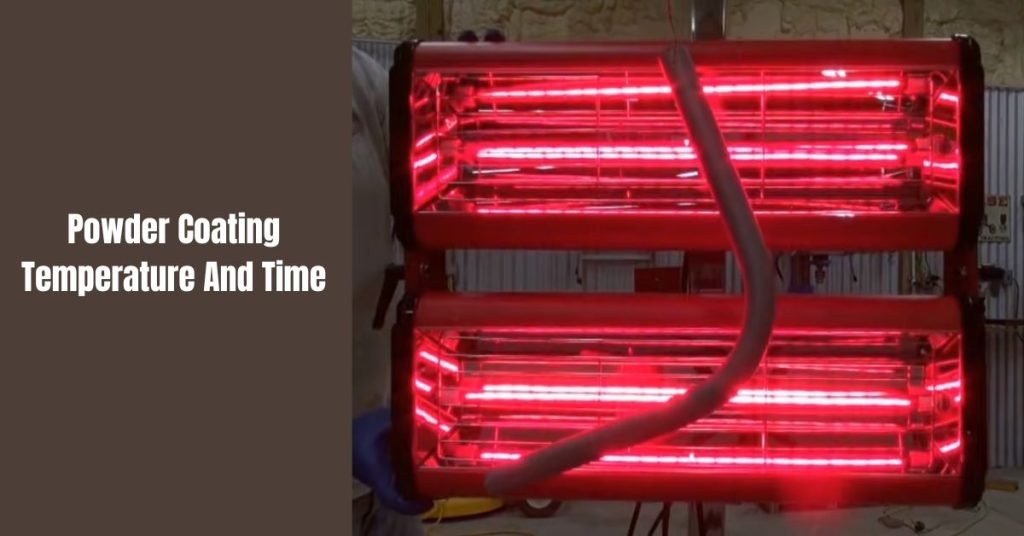
Powder Coating Temperature And Time
The optimum temperature and time for powder coating are determined by the type of powder and substrate being used.
To ensure a successful outcome, the initial step is to preheat the object that needs to be coated. This eliminates any moisture and prepares the surface for optimal adhesion. The recommended temperature for preheating typically falls in the range of 350°F to 450°F, depending on the type of material.
Once the preheating is complete, the next crucial step is the application of the powder coating material. The object is coated with a fine powder of pigment and resin particles. The temperature must be precisely controlled during this process, usually around 380°F to 400°F.
Maintaining this temperature for the required time ensures the powder melts and forms a uniform, smooth finish. The curing time typically varies between 10 to 30 minutes, depending on the specific powder coating material and the desired outcome.
Choosing The Right Temperature And Time Combination
When it comes to achieving the perfect finish with powder coating, selecting the right temperature and time combination is crucial. The curing process of powder coating involves applying heat to the coated substrate, allowing it to chemically react and form a protective and durable layer.
Understanding the factors that influence this process and how to determine the ideal temperature and time combination for specific coatings and applications is essential for achieving optimal results.
Factors To Consider When Selecting Powder Coating Temperature And Time
Selecting the right temperature and time combination for powder coating is a critical aspect of the process that directly influences the quality and longevity of the finish. To make informed decisions and achieve the best results, it’s essential to consider several key factors. These factors play a crucial role in determining the effectiveness and durability of the powder coating.
1. Type of Coating
The first factor to consider is the type of coating being used. Powder coatings come in various formulations, each with its unique characteristics and requirements. Some coatings, like epoxy and polyester, may have different optimal temperature and time settings. It’s crucial to align the temperature and time with the specific properties of the coating material to ensure proper curing and adhesion.
2. Thickness of the Coating
The thickness of the coating is another vital factor. Thicker coatings often require higher temperatures and longer curing times to ensure complete and even curing. Thinner coatings, on the other hand, may need lower temperatures and shorter curing times. Achieving the desired coating thickness without under or over-curing is a delicate balance that depends on the thickness of the application.
3. Desired Adhesion and Hardness
The level of adhesion and hardness you desire in the finished product plays a significant role in temperature and time selection. Higher temperatures and longer curing times can lead to increased adhesion and hardness. This is particularly important in applications where the coating must withstand significant wear and tear, such as automotive or industrial settings.
4. Substrate Material
The material you’re coating, also known as the substrate, can greatly influence the temperature and time requirements. Different materials have varying thermal properties and may react differently to the curing process. For instance, coating aluminum may require different temperature and time settings compared to coating steel. It’s essential to account for the specific characteristics of the substrate material in your selection.
5. Manufacturer Guidelines
Manufacturers of powder coating materials often provide detailed guidelines and recommendations for the ideal curing temperature and time for their products. These guidelines are based on extensive testing and research, making them valuable resources for achieving optimal results. Always consult the manufacturer’s instructions and specifications to ensure you’re within the recommended parameters.
6. Environmental Considerations
Environmental factors can also influence your decision. If you aim for an eco-friendly approach, you might opt for lower temperatures and shorter curing times, which can reduce energy consumption and emissions. This is especially important in today’s world, where sustainability is a significant concern.
Ideal Temperature And Time Combination For Specific Coatings And Applications
Determining the ideal temperature and time combination for specific coatings and applications requires careful experimentation and testing.
Manufacturers of powder coatings typically provide guidelines and temperature ranges for their products, which can serve as a starting point. Factors such as desired coating thickness, curing time limitations, and specific application requirements may require adjustments.
Here are some common coatings and applications, discussing the optimal temperature and time settings for each.
Epoxy Coatings for Appliances
Temperature: 375°F to 400°F Time: 15 to 20 minutes
Epoxy coatings are commonly used for appliances like refrigerators and ovens. The ideal temperature range for epoxy coatings falls between 375°F and 400°F, with a curing time of 15 to 20 minutes. This combination ensures a durable and attractive finish that can withstand the demands of everyday use.
Automotive Powder Coating
Temperature: 400°F to 450°F Time: 20 to 30 minutes
Automotive applications require a robust and long-lasting finish. For automotive powder coating, temperatures ranging from 400°F to 450°F are recommended, along with a curing time of 20 to 30 minutes. This combination results in a tough coating that can resist the harsh conditions of the road.
Architectural Coatings for Outdoor Use
Temperature: 375°F to 400°F Time: 10 to 15 minutes
Architectural coatings, often used for outdoor structures like fences and railings, need to withstand exposure to the elements. The ideal temperature range for such coatings is 375°F to 400°F, with a shorter curing time of 10 to 15 minutes. This combination provides excellent protection and aesthetics.
Custom Motorcycle Parts
Temperature: 375°F to 400°F Time: 15 to 20 minutes
Custom motorcycle parts require precision and a flawless finish. The recommended temperature range for these parts is 375°F to 400°F, and the curing time should be around 15 to 20 minutes. This combination ensures that your motorcycle components look as good as they perform.
Furniture Coatings
Temperature: 350°F to 375°F Time: 15 to 25 minutes
Furniture coatings demand an attractive appearance along with durability. The optimal temperature range for coating furniture is 350°F to 375°F, with a curing time of 15 to 25 minutes. This combination results in a beautiful and tough finish that can withstand daily wear and tear.
Aerospace Applications
Temperature: 400°F to 450°F Time: 20 to 30 minutes
In the aerospace industry, precision and performance are non-negotiable. For aerospace applications, the recommended temperature range is 400°F to 450°F, with a curing time of 20 to 30 minutes. This combination ensures a finish that meets the stringent requirements of this sector.
Fine Detail Work
Temperature: 375°F to 400°F Time: 10 to 15 minutes
When it comes to fine detail work on objects like sculptures or intricate metalwork, a lower temperature range of 375°F to 400°F and a shorter curing time of 10 to 15 minutes are typically suitable. This combination allows for precision and preserves intricate details.
High-Temp Coatings
Temperature: 400°F to 450°F Time: 20 to 30 minutes
For high-temp coatings, such as those used in the marine industry or for heavy machinery, a higher temperature range of 400°F to 450°F and a curing time of 20 to 30 minutes are essential. This combination ensures durability in demanding environments.
Optimizing Energy Consumption
Efficient powder coating processes are not only environmentally friendly but can also lead to significant reductions in operational costs. One crucial aspect of optimizing energy consumption is understanding the relationship between temperature, time, and energy efficiency.
The Relationship Between Temperature, Time, And Energy Efficiency
Temperature and time are two critical factors that directly impact the energy efficiency of a powder coating process. The higher the temperature and longer the curing time, the more energy is required to achieve the desired coating results. It’s important to strike a balance between energy efficiency and coating quality.
Strategies For Reducing Energy Consumption In Powder Coating Processes
To minimize energy consumption in powder coating processes, several strategies can be implemented:
Implement intelligent control systems that accurately measure and control the temperature during the curing process, ensuring it remains within the optimal range. This prevents unnecessary temperature fluctuations and reduces energy wastage.
Utilize advanced insulation materials to improve the thermal efficiency of the curing oven. Proper insulation helps retain heat, reducing the energy required to maintain the desired curing temperature.
Consider using more energy-efficient equipment, such as infrared curing systems or convection ovens with improved insulation and temperature control features. These technologies can reduce energy consumption while ensuring consistent and reliable curing results.
Implement effective airflow management within the curing oven to ensure uniform heat distribution. This prevents hotspots and reduces the overall curing time, further enhancing energy efficiency.
Perform regular maintenance and cleaning of the powder coating equipment to ensure optimal performance. Regular upkeep prevents energy loss resulting from equipment inefficiencies or malfunctions.
The Benefits Of Using Lower Temperatures And Shorter Curing Times
Using lower temperatures and shorter curing times in powder coating processes can offer several advantages:
- Reduced energy consumption, leading to cost savings and improved environmental sustainability.
- Decreased risk of thermal degradation or discoloration of certain materials, particularly heat-sensitive substrates.
- Increased productivity due to reduced curing times, allowing for faster throughput and shorter production cycles.
- Potential for increased flexibility in scheduling, as shorter curing times enable quicker product turnaround.
- Limited impact on surrounding areas by minimizing heat emissions and reducing the need for extensive ventilation systems.
While lower temperatures and shorter curing times present numerous benefits, it’s crucial to evaluate the specific coating requirements and performance standards before making any adjustments.
Achieving Consistent Coating Quality
When it comes to powder coating, achieving consistent coating quality is paramount. The temperature and time during the powder coating process play critical roles in determining the durability and adhesion of the coating.
Now, we will explore the effect of temperature and time on coating thickness and adhesion, the techniques for ensuring uniform coating application at different temperatures, and how to control dwell time to prevent defects like overcuring or undercuring. We will also provide an overview of quality control measures throughout the powder coating process.
The Effect Of Temperature And Time On Coating Thickness And Adhesion
Temperature and time significantly impact the quality of powder coating. The powder melts and fuses into a continuous film when exposed to the proper curing temperature. Too high a temperature can result in overcuring, leading to reduced coating thickness and decreased adhesion. On the other hand, insufficient temperature may cause undercuring, resulting in a weak and easily damaged coating.
- Inadequate Curing: Below recommended temperature, Insufficient time.
- Optimal Curing: Recommended temperature, Sufficient time.
- Overcuring: Above recommended temperature, Excessive time.
It is crucial to follow specified temperature and time guidelines to achieve the desired coating thickness and adhesion. Additionally, factors like the object’s size, shape, and color can influence the curing requirements, so it is essential to consult the powder coating manufacturer’s recommendations for optimal results.
Techniques For Ensuring Uniform Coating Application At Different Temperatures
Ensuring uniform coating application is vital to achieve consistent coating quality. When working with varying temperatures, here are some techniques to ensure uniformity:
Preheating the substrate: Preheating the substrate prior to powder coating helps to reduce temperature differentials within the material. This technique promotes consistent melting and flow of the powder, resulting in an even coating thickness.
Using proper equipment: Utilizing equipment designed specifically for powder coating, such as electrostatic sprayers or fluidized bed systems, ensures consistent powder application regardless of temperature variations.
Applying multiple thin coats: Instead of applying one thick coat, applying multiple thin coats allows for better control of the coating thickness. This technique also reduces the risk of defects associated with uneven curing caused by temperature variations.
By implementing these techniques, you can maintain uniform coating application, irrespective of temperature fluctuations.
Controlling Dwell Time To Prevent Defects Like Overcuring Or Undercuring
The dwell time, which refers to the duration of exposure to the curing temperature, is critical in preventing defects like overcuring or undercuring. It is essential to monitor and control the dwell time throughout the powder coating process.
If the dwell time is too short, the powder coating may not reach its optimal cure, resulting in undercuring. On the contrary, dwell times that are too long can lead to overcuring, causing the coating to become brittle, discolored, and prone to cracking.
To control dwell time effectively:
- Invest in temperature monitoring equipment to accurately measure the cure temperature.
- Maintain consistent line speed to ensure consistent exposure time. Adjusting the line speed helps regulate the dwell time, offering better control over the curing process.
- Regularly calibrate and maintain curing ovens to ensure they are providing accurate and consistent temperatures.
By closely monitoring and controlling the dwell time, you can prevent defects associated with overcuring or undercuring, ensuring a high-quality powder coating finish.
An Overview Of Quality Control Measures Throughout The Powder Coating Process
The powder coating process involves multiple stages where quality control measures are essential. Here is an overview of the key quality control measures:
Surface preparation: Proper cleaning and pre-treatment of the substrate ensures a clean surface for optimal coating adhesion and minimizes the risk of defects.
Application technique: Employing suitable equipment and techniques, such as electrostatic spraying or fluidized bed systems, guarantees consistent and uniform powder application.
Curing process: Monitoring and controlling the curing temperature, dwell time, and line speed ensure proper curing and prevent defects like overcuring or undercuring.
Inspection: Conducting regular inspections throughout the process helps identify any defects or inconsistencies. This allows for timely corrections and ensures a high-quality coating finish.
Implementing these quality control measures throughout the powder coating process enhances consistency and reliability, resulting in a durable and visually appealing coating.
Extending The Lifespan Of Powder Coating Equipment
As a powder coating professional, it is crucial to understand the impact of temperature and time on the lifespan of your equipment. Proper maintenance and cleaning procedures, combined with the right temperature and time settings, can significantly extend the life of your powder coating equipment.
By implementing strategies to reduce wear and tear, you can minimize downtime and maximize productivity. Let’s dive in!
The Impact Of Temperature And Time On Equipment Wear And Tear
When it comes to powder coating, the temperature and time settings play a crucial role in achieving a durable and high-quality finish. Improper temperature and time settings can lead to excessive wear and tear on your equipment.
High temperatures and prolonged exposure can cause premature aging of oven components, such as heating elements and conveyor chains. This can result in frequent breakdowns and the need for costly replacements.
On the other hand, insufficient temperature and time can result in incomplete powder curing, leading to poor adhesion and reduced durability of the coating. Finding the right balance is essential to ensure optimal equipment performance and longevity.
Proper Maintenance And Cleaning Procedures To Maximize Equipment Lifespan
To prolong the lifespan of your powder coating equipment, regular maintenance and cleaning are essential. Neglecting these tasks can lead to a buildup of overspray, contaminants, and debris, which can affect the performance and efficiency of your equipment.
Here are some proper maintenance and cleaning procedures you should follow:
- Regularly inspect and clean your spray booth, filters, and ventilation system.
- Remove any excess powder from your equipment after each coating cycle.
- Check and clean the powder delivery system, including hoses, guns, and nozzles.
- Inspect and lubricate moving parts to prevent friction and optimize performance.
- Keep your temperature control devices calibrated and accurate.
Common Issues Caused By Improper Temperature And Time Settings
Improper temperature and time settings can lead to various issues that affect the performance and lifespan of your powder coating equipment. Some common problems include:
- Poor adhesion and coating defects
- Incomplete curing and reduced durability
- Uneven coating thickness
- Excessive wear and tear on oven components
- Frequent breakdowns and increased downtime
By understanding these common issues, you can take preventive measures and adjust your temperature and time settings accordingly.
Strategies For Prolonging The Life Of Oven Components And Reducing Downtime
To minimize wear and tear on oven components and reduce downtime, consider implementing the following strategies:
- Optimize temperature and time settings based on the specific requirements of the powder coating material.
- Regularly inspect and replace worn-out or damaged oven components, such as heating elements and conveyor chains.
- Implement a preventive maintenance schedule to address potential issues before they escalate.
- Train your operators on proper equipment usage and maintenance procedures.
- Document and analyze equipment performance to identify areas for improvement and optimize efficiency.
By implementing these strategies, you can extend the lifespan of your powder coating equipment, minimize downtime, and ensure consistent, high-quality results.
Frequently Asked Questions Of Powder Coating Temperature And Time
How Long Does It Take For Powder Coat To Dry?
Powder coat typically dries within 20 minutes to an hour. The exact drying time depends on factors like the type of powder used, thickness of the coating, and the curing temperature. It is essential to follow the manufacturer’s instructions for the best results.
What Temperature Can Powder Coating Take?
Powder coating can withstand high temperatures, typically ranging from 300 to 450 degrees Fahrenheit. It is designed to endure heat, ensuring durability and longevity for the coated surface.
What Oven Setting Is Needed For Powder Coating?
For powder coating, the oven setting required is typically around 400 to 450 degrees Fahrenheit. This temperature allows the powder to melt and form a smooth, durable finish on the surface.
Can You Cook Powder Coat Too Long?
No, you should not cook powder coat for too long as it can result in overheating and damage. It’s important to follow the recommended time and temperature guidelines provided by the manufacturer to ensure proper curing and avoid any potential issues.
Be cautious and adhere to the instructions for best results.
Final Thoughts
Understanding the importance of temperature and time in powder coating is crucial for achieving the best results. By properly adjusting these variables, you can enhance adhesion, color consistency, and overall durability of the coating. Remember to consult the manufacturer’s guidelines and experiment with different combinations to find the ideal temperature and time for your specific project.
With careful consideration of these factors, you can achieve a flawless finish that meets the highest standards of quality and performance.