UV cured powder coating is an innovative technology that is gaining popularity across a range of industries. But what exactly is it, and why are more and more companies switching to this new powder coating method?
In this comprehensive guide, we’ll cover everything you need to know about UV cured powder coating – from how it works to its advantages over traditional powder coating, applications, the curing process and equipment needed, costs, and more. By the end, you’ll have a solid understanding of this emerging powder coating technology and whether it could benefit your business.
So let’s get started!
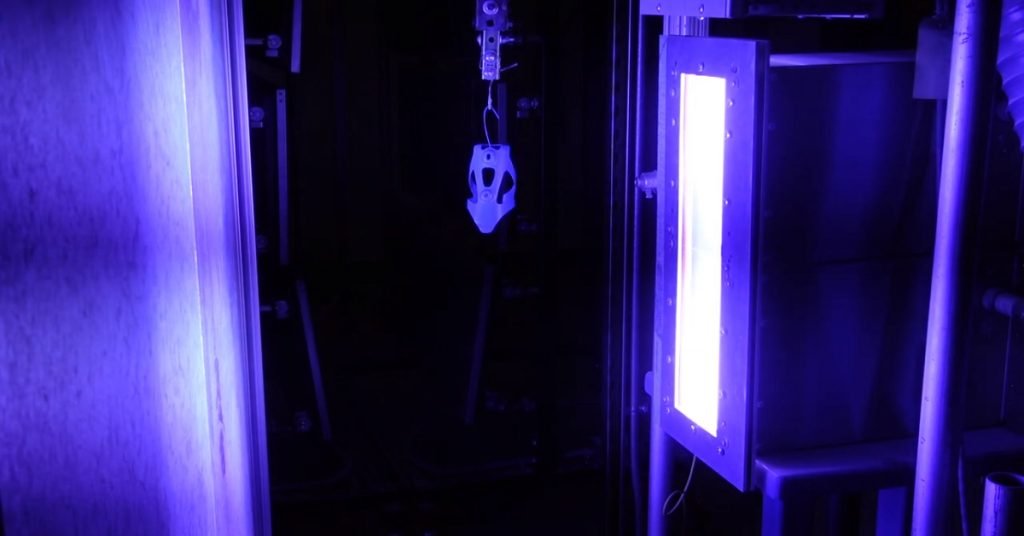
What is UV Cured Powder Coating?
UV cured powder coating is a type of powder coating that uses ultraviolet light to cure and harden the coating, rather than heat like traditional powder coatings.
It works by using powder coating materials that are formulated to react under UV light, starting a chemical reaction that creates the hard, durable finish. This reaction can occur much faster than thermal curing, and at significantly lower temperatures.
The technology first emerged in the 1990s as an alternative to standard powder coating and has continued gaining traction since then. It offers a high-quality finish while avoiding some of the limitations of traditional powder coating methods.
Key Benefits of UV Cured Powder Coating
There are several important benefits that UV cured powder coatings provide over traditional powder:
Faster Processing and Curing Times
One of the biggest advantages of UV powder coating is the faster curing time.
While standard powder coatings may require 15-25 minutes oven time to fully cure, UV powders can cure in just seconds with the right UV equipment. This speedy process allows for much higher production rates and throughput.
Parts can be coated and quickly moved on to the next stage of production, assembly, packaging, or shipping. For manufacturers doing high volume runs, the time savings really add up.
Lower Curing Temperatures
Traditional powder coatings typically cure at temperatures between 300-400°F. But UV powders can cure at much lower temps, often between 140-180°F.
This lower temperature is beneficial when coating heat-sensitive materials like plastics, carbon fiber, wood products, and MDF board. It avoids warping or damage issues.
Lower curing temperatures also mean less energy consumption for curing ovens and HVAC systems, reducing operating costs.
Smooth, Durable, High-Gloss Finishes
UV cured powder coatings are engineered to flow out smoothly when exposed to UV light, minimizing the orange peel effect that can plague traditional powder finishes.
The technology can produce coatings with a gloss level of 90+ GU, similar to liquid and automotive paints. This allows metal, plastic, and wood products to take on a clear, glass-like finished look.
And UV powder films are known for their hardness, durability, and chemical/corrosion resistance – equal to or better than standard powder.
Environmentally Friendly Process
With UV powders, there are no solvents or VOCs released during curing since no heat is involved. The UV curing process consumes very little energy compared to running large ovens or burners.
Many UV powder formulations also rely on renewable raw materials like plant-based resins. And they can reduce the amount of harmful chemicals like TGIC powder coatings require.
Overall, UV curing results in a more eco-friendly coating process – an increasingly important factor for businesses and consumers alike.
Coating Heat-Sensitive Materials
We’ve mentioned how UV powders allow lower temperature curing. This makes them uniquely suited for coating heat-sensitive substrates that couldn’t withstand traditional powder coating.
Materials like plastics, composites, wood, and MDF can now be powder coated. Even heat-sensitive metals like aluminum and magnesium alloys are candidates with UV curing.
This widely expands the number of products and components that powder coating can be used on.
Wider Range of Colors and Special Effects
Standard powder coating colors are limited by the need for thermo-stability during oven curing. But UV powders are free of this constraint, since no heat is involved.
This allows UV powders to achieve a broader range of colors and glosses. Metallic, pearl, and iridescent finishes are also possible.
Manufacturers can produce brightly colored products that stand out on retail shelves and showroom floors with UV powder technology.
Industries Using UV Cured Powder Coating
With all these benefits, UV cured powder coating has been adopted across a diverse range of industries and applications:
Automotive
UV powder use is growing in automotive for coating wheels, trim pieces, light housings, and other components. The fast cure works well in high production environments while delivering smooth, durable finishes.
It also enables more plastic and composite automotive parts to be powder coated.
Appliances and Consumer Goods
Appliance manufacturers take advantage of UV powders for oven doors, refrigerators, laundry machines, and other products. It allows eye-catching colors and fewer finish flaws on plastic components.
A wide range of consumer products also rely on UV powder for a protective finish – electronics, sporting equipment, garden tools, furniture, shelves, and more.
Architectural
Metal roofing, window frames, doors, railings, and building panels are now candidates for UV powder coating’s protective finish and uv/corrosion resistance. It meets the demanding requirements of the architectural industry.
Bicycles and Motorcycles
Bike makers use UV powders to coat alloy wheel rims and frames. The fast processing suits high production volumes. And the low temperature curing prevents damage to lightweight alloys.
Motorcycle manufacturers similarly rely on UV coatings for wheels, fairings, fuel tanks, side panels, and alloy engine parts.
Furniture
Tables, chairs, office furniture, kitchen cabinets, and shelving benefit from UV powder for an attractive high-gloss or matte look. It can coat heat-sensitive woods and composites. And the finish resists scratches, chips, and water damage.
How Does UV Powder Curing Work?
Now that we’ve covered the benefits and applications of UV cured powder coating, let’s look at how the curing process actually works.
UV powder contains specialized resins and pigments designed to crosslink into a cured film when exposed to ultraviolet light.
When the powder particles are sprayed onto a substrate through electrostatic guns, they remain as a dry powder film initially. The object then enters a curing unit where high intensity UV lamps emit light at the proper wavelengths to activate the UV resins.
This creates free radicals within the powder particles, initiating crosslinking between polymer chains. The powder flows out and rapidly hardens within seconds into a smooth, hard film.
Two main curing methods are used – conveyor systems and integrated box or chamber units:
- Conveyor – Objects pass under a series of UV lamps on a conveyor belt. Allows continuous curing for high volumes.
- Box/Chamber – UV lamps are built into an enclosed box or chamber. Useful for coating 3D objects.
UV LED curing systems are also growing in popularity – more on that next.
The prerequisites before coating are similar to standard powder coating – parts must be thoroughly cleaned and pretreated for optimal adhesion. The powder coating guns and recovery systems are also the same.
It’s only the curing step that differs with UV activated powders.
UV LED Curing Systems
Early UV curing relied on mercury vapor lamps to generate UV energy. But UV LED technology is rapidly overtaking these older methods with several important benefits:
Faster Curing – UV LEDs initiate crosslinking faster than mercury bulbs. Some coatings can cure in under 10 seconds. This allows even higher throughput.
Lower Energy Use – LEDs convert energy to UV light more efficiently, reducing power needs by 50% or more. This cuts energy costs significantly.
Less Substrate Heating – LED curing avoids infrared heat associated with mercury bulbs, keeping substrate temperatures lower. Important for heat-sensitive materials.
Longer Lamp Life – LED lamps last up to 20 times longer than mercury bulbs – up to 20,000 hours vs 2,000 hours for mercury. This reduces maintenance.
Compact Size – LED curing units are much smaller than conventional UV booths. This saves valuable factory floorspace.
Better Process Control – LED output can be instantly adjusted. This gives finer control over the curing process.
Many factories are now switching to LED systems as the costs continue to fall. But mercury UV is still used as well.
UV Powder Coating Equipment Needed
Here is an overview of the primary equipment needed for UV powder coating:
- Pretreatment System – Cleans and prepares substrates for optimal coating adhesion. Can include washers, degreasers, conversion coatings.
- Powder Coating Booth – Contains the spray guns and powder overspray. Provides worker safety and cleanliness.
- Powder Coating Guns – Electrostatic and tribo guns apply the powder coating to electrically ground parts.
- UV Curing Unit – Provides UV exposure to cure the powder coating. This is the key element unique to UV powder processes. Mercury, UV LED, or other systems can be used.
- Conveyors – Used to move parts through the wash, coat, and cure process steps.
- Part Fixtures – Holds small parts to be coated, allowing all sides to be powder coated as needed.
- Controls – PLCs and software to operate the conveyors, UV curing, guns, and other equipment.
- Air Compressors & Piping – Provides compressed air to operate the powder guns.
- Environmental Systems – Air make up units, exhaust fans to manage air quality.
- Masking – Tapes, shields, or masks may be required to block off areas not to be coated.
Much of this equipment is the same as used for traditional powder coating. Only the curing unit itself differs for UV powder. This allows many factories to utilize existing infrastructure and simply add on UV curing capabilities.
Costs of UV Cured Powder Coating
Here is an overview of the costs associated with UV powder coating:
Equipment
The primary investment will be the curing equipment itself:
- UV Conveyor Unit – $50,000 to $150,000+
- UV Chamber/Box Unit – $20,000 to $60,000
- UV LED System – $25,000 to $80,000
Other equipment like pretreatment, booth, guns, may involve less investment if a powder line already exists. But budget $125,000 to $400,000+ for a complete automated UV capable system.
Powder Materials
UV powders currently run 20-50% higher in cost than traditional powder coatings. However, price gaps are narrowing as volumes increase. Expect $3-6/lb for UV powder.
Energy
UV curing consumes far less energy than thermal ovens. Cost savings of 50-75% are typical.
Labor
Higher throughput with UV powders offsets labor costs. And eliminating post-processing like sanding or rework further reduces labor.
Rejects/Rework
UV powder produces fewer rejects and warranty claims. Scrap and rework costs drop substantially.
Maintenance
UV curing equipment requires minimal maintenance other than occasional lamp replacement. Costs are minor.
Space
A UV line may require less factory space since ovens are eliminated. This saves on overhead.
Summary
The equipment investment may seem high initially. But consider the total cost savings from faster processing, reduced labor, energy and maintenance. Many find UV powder delivers a 1-2 year payback.
Applying UV Powder Coatings
The application process itself for UV powders is very similar to standard powder coatings:
1. Surface Preparation
Substrate surfaces must be thoroughly cleaned and pretreated for proper adhesion. This typically involves:
- Alkaline Washing to Remove Oils/Soils
- Rinsing
- Phosphating or Chromating to Improve Adhesion
- Additional Rinsing
- Drying
2. Powder Application
UV powders are applied using standard electrostatic spray (ESG) or tribo guns within a powder coating booth. Uniform, even films are needed for proper curing.
3. Curing
The coated parts enter the UV curing unit where high intensity UV light initiates rapid crosslinking. Curing happens within seconds.
4. Testing and QC
Cured films undergo testing for proper film thickness, adhesion, gloss, smoothness, and other properties per specifications.
5. Packaging
QC approved finished goods are packaged and prepared for shipping.
It’s really only the curing step that differs from a traditional powder coating process. And switching to UV opens up many new substrate and finish possibilities.
UV Powder Coating on Wood and MDF
One of the most useful applications of UV powder coating is on wood products, furniture, and medium density fiberboard (MDF).
Traditional powder couldn’t be used on most woods or MDF since the 300°F+ curing temperatures would cause damage, burns, or outgassing problems.
But with UV powders that cure below 180°F, it’s now possible to powder coat wood products with excellent results:
Preparation – Woods must be sanded smooth and cleaned to remove oils, sap, dirt. Some bleaching may improve results on oak or cedar. MDF requires less prep.
Sealing – The best practice is to seal the wood first before coating. This prevents outgassing that causes bubbles or defects in the film. A thin sealer is sprayed or rolled on.
Coating – UV powders can then be applied electrostatically or tribo charged. Edge coaters allow wraparound coverage.
Curing – Low temperature UV curing prevents substrate damage. Curing just the sealer first improves flow and adhesion.
Finishing – Light sanding or scuffing between coats improves smoothness. Topcoats enhance durability and aesthetics on wood.
The result is beautiful, durable powder coated woods for furniture, cabinets, shelving, and more. And manufacturers save costs over varnishes, stains, or laminates while providing creative looks.
MDF in particular takes UV powder beautifully. The makeup of MDF prevents outgassing issues, minimizing prep needed. MDF offers a smooth canvas for colored coats in high-gloss or matte textures.
Challenges and Limitations of UV Powder
While UV cured powder offers many benefits, it also comes with some challenges and limitations to consider:
Higher Costs – As mentioned, UV powders currently cost more than traditional powders – up to 50% higher depending on chemistry and volumes. The curing equipment are also major investments. This can deter smaller shops.
Training – Employees accustomed to traditional powder coating need training to successfully switch to UV-cured systems. There are nuances to the process that require education.
Substrate Cure Testing – Coating new or unknown substrates requires testing to confirm the curing process doesn’t cause damage. This is especially important for heat-sensitive materials.
UV Exposure – Operators need proper protection from UV radiation, including tinted visors/glasses, gloves, and skin covers. Unprotected exposure can cause health hazards. Proper facility safeguards are a must.
Color Limitations – While UV powders offer a wider color range than standard powder, limitations still exist, especially with darker or blended colors. The UV light must adequately penetrate the coating to activate curing.
Adhesion Testing – Cured UV powder films require testing on new substrates to verify proper adhesion. Pretreatment processes may need adjustments to optimize adhesion.
Code Approvals – Using UV coatings on products like appliances will require getting UL, AAMA and other approvals. This process can take months.
Should You Consider UV Cured Powder Coating?
If you’re considering a move to UV cured powder technology, first look at these key factors:
- Production Volume – High output shops gain the most from UV powders increased throughput. Lower volumes may not justify the investment.
- Product Mix – Do you regularly coat plastics, wood, or heat-sensitive metals? These stand to benefit the most from UV’s low temp curing.
- Reject Rate – UV powders should lower rejects. Calculate potential scrap savings in your process.
- Color Offerings – Are bright colors or special effects important to your products? UV opens up more possibilities.
- Certifications – Will the switch to UV delay getting re-approvals? Account for this timeframe.
- Operator Skill – Evaluate your team’s ability to adapt to new UV processes with proper training.
Also talk to trusted UV powder suppliers about options. They can help assess if UV meets your needs and provide guidance on getting started.
With analysis of these factors, you can determine if UV powder coating aligns with your manufacturing goals. The technology presents exciting new opportunities – but it also requires due diligence before diving in.
The Future of UV Powder Coating
UV cured powder coating has already impacted a wide range of industries since its inception. But the technology still has room for expansion as costs come down and capabilities improve.
Here are several trends that will shape UV powder’s future growth:
- Lower equipment costs expanding adoption to more small/medium businesses
- UV LED curing reaching higher intensities to cure more coating chemistries
- Hybrid coatings combining UV powders with other polymers for wider use
- Formulations with greater heat resistance, chemical resistance, and durability
- Lower film thicknesses for reduced material costs
- Multi-layer film technology to achieve special effects
- Integration of UV sensors and controls for automation and data tracking
- Expanding color palettes and gloss ranges
- Approvals for UV use on more commercial and consumer end products
- Wider adoption across automotive, aerospace, medical, and marine industries
- Growth in Asia, Africa, and South America as global manufacturing expands
- More environmentally friendly powder chemistries
UV powder coating enables finishes that weren’t possible just a decade ago. We should expect the technology to rapidly progress in the coming years as research brings new innovations.
Final Thoughts
UV cured powder coating provides game-changing advantages for many manufacturing processes due to its fast cure, smooth finish, low temperature requirements, and ability to coat plastics and composites. Companies dealing with heat-sensitive substrates or high production volumes stand to benefit the most from transitioning to UV curing. While requiring some investment, the overall quality, efficiency, and cost gains make it very compelling for the right applications.